Electrical Programmable Fuse (eFUSE) is a One-Time-Programmable (OTP) solution for System-on-Chip (SoC) Integration. Programming of an eFUSE ROM block (figure 1a) is normally done by driving relatively high current pulses through its submicron dimension fuse structures (figure 1b). The long term reliability of the eFUSE is obviously of great importance for the normal operation of the controller as well as the integrated component and system it is embedded in.
In this work we present a method of finding the optimized programming (fuse blowing) conditions for the effective and reliable functionality of the fuse block. This approached has already been successfully implemented for Seagull, one of the recent ASIC controllers designed at SanDisk Omer for the iNAND products.
Introduction:
The correct trimming of the voltage, as well as the resulting current and the pulse duration (figure 2) of the blowing pulse is critical for achieving an accurate and reliable code during operation of the product in the field. The problem is that programming pulse voltage and duration, as provided by the IP vendor, might not always be adequate for a specific design and sometimes a fuse that is detected as correctly programmed by the tester during the programming stage fails in the field causing malfunction of the customer’s device!
The conventional approach is to apply a long period high temperature stress (HTOL) on the burnt fuses and check if they retain their logic state. However, this is a time consuming approach which requires a large sample size and might result false alarms due to the statistical nature of this method!
Theoretical background:
In principle, each fuse element is composed of a high resistive poly Si line, covered by a lower resistance thin Silicide layer, through which the majority of the programing current flows. At spec programming conditions this current is supposed to cause an instantaneous peak of heat resulting burn out of the narrow section (“neck”) of the Poly Si line together with the Silicide film (figure 1b).
We found that if the electrical programming conditions are non-optimized the local heat generated is insufficient, so the silicide layer burns while the narrow poly line does not! However, the fuse might appear to be electrically “open” due to its relatively high resistivity, thus considered as a properly programmed fuse! The problem is that the thin silicide layer in this improperly burnt fuse might “reconnect” under high temperature operating conditions of the device in the field, resulting the programmed fuse to switch its state!
Details of proposed method and experimental results:
We propose to investigate the physical condition of the fuses using Scanning Electron Microscopy (SEM) and Focused Ion Beam (FIB) systems. Figure 3 shows a set of fuses that were programmed at various electrical programming conditions.
Since it is difficult to identify the fuse state from the top view a cross section of the fuse by the FIB is performed. X-section of a properly burnt fuse is shown in figure 4, showing the cut of the narrow section of the poly line while in figure 5 it is still connected!
Summary:
We present a quick and reliable method to verify the correct programming conditions of OTP eFUSEs. It is proposed to apply this approach, which was successfully implemented on the Seagull controller, during the qualification stage of each ASIC controller.
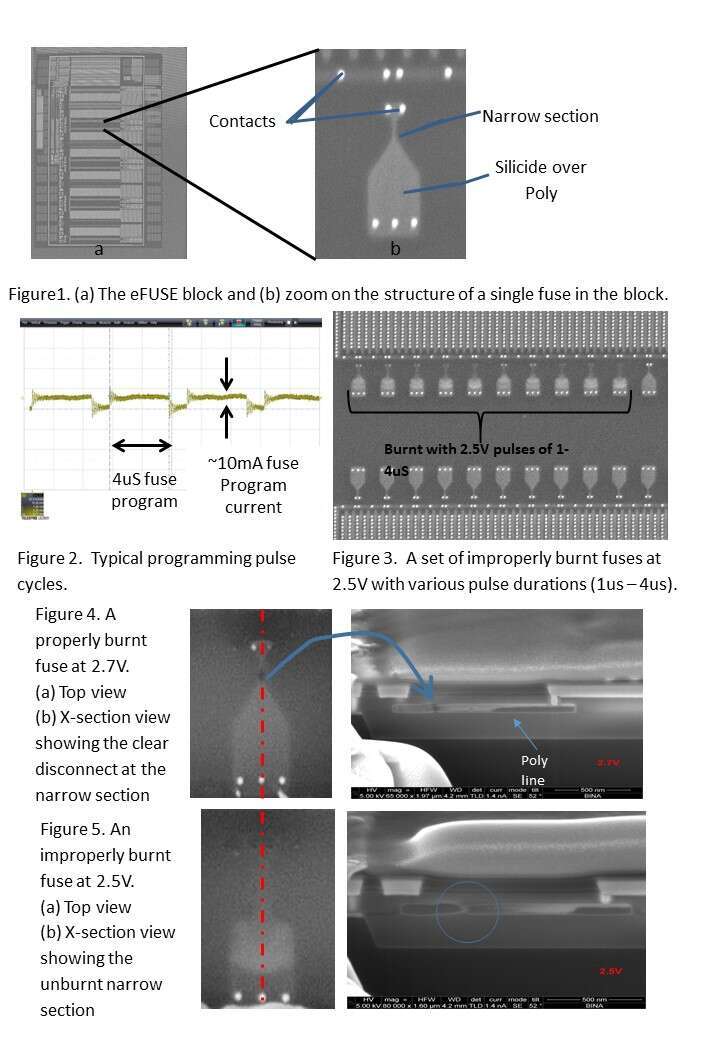