Highly nonlinear waveguides are fabricated through deposition of chalcogenide glass into pre-patterned trenches in a silica cladding. No processing of the chalcogenide glass is required. Four-wave mixing is demonstrated with nonlinear coefficient of 6.5±1 [Wm]-1.
Chalcogenide glasses (ChGs) are a favorable material platform for on-chip, all-optical signal processing applications, due to their pronounced nonlinearities, broad transparency and photo-sensitivity [1]. Examples include time-domain de-multiplexing of high-rate data based on four-wave mixing (FWM) [2], microwave-photonic filtering of radio-frequency waveforms using stimulated Brillouin scattering (SBS) [3], and many more. The most widely-employed ChG composition is arsenic tri-sulfide (As2S3). Nonlinear propagation coefficients as high as 10 [Wm]-1 have been demonstrated in planar As2S3 waveguides [4]. The devices were fabricated based on dry etching of the ChG core layer [5]. Although low propagation losses could be achieved [5], the etching process remains difficult to implement due to the relative instability of ChGs. In addition, an individual protocol must be developed for each ChG composition, and the etching of the ChG layer following its deposition is not fully compatible with the fabrication of CMOS electronics.
In this work we propose and demonstrate an alternative method for the fabrication of highly-nonlinear ChG waveguides with small cross-sectional areas. The waveguide patterns are first defined as narrow, isolated and comparatively deep etched trenches in a silica lower cladding layer. A ChG layer is deposited to form a core region that partially fills the etched trenches, as a final process step. The ChG core is surrounded by silica on three sides. The fabrication procedure relies on well-established etching of silica, supports the deposition of any ChG composition, and requires no processing of the ChG core itself. Lastly, the ChG-in-silica structure guides both optical and hyper-sonic acoustic modes with tight confinement and large spatial overlap. Such confinement is a pre-requisite for efficient opto-mechanical interactions [6]. The platform therefore holds much promise for future demonstrations and applications of SBS on-chip.
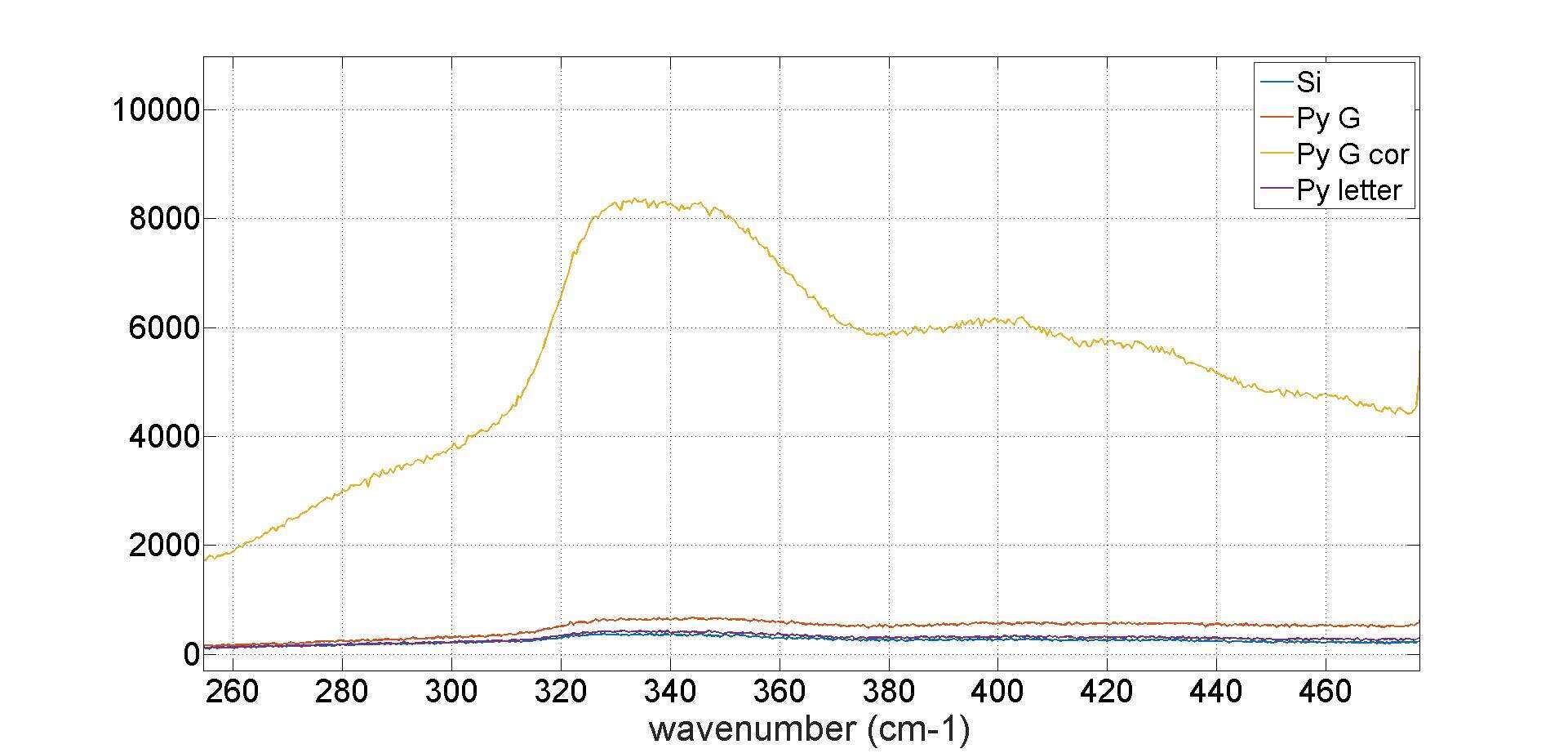
Figure 2. Left – Top-view microscope image of a chalcogenide glass-in-silica waveguide alongside an input lensed fiber. Red light is coupled into the waveguide for illustration purposes. Right – Normalized optical power spectral density of light at the output of a 4.6 mm-long waveguide. Two four-wave mixing products are observed to the sides of two incident pump waves.
2. Device Fabrication and Characterization
The fabrication process of ChG-in-silica waveguides is illustrated in Fig. 1 (left). Waveguides are fabricated in silica-on-silicon wafers, with a 3.5 μm-thick layer of silica (panel (a)). Patterns are first defined in an AZ-1505 photo-resist layer (panel (b)), through standard UV photo-lithography and subsequent developing (panel (c)). The inverse pattern is then transferred onto an 80 nm-thick chromium hard mask layer (panel (d)), using a lift-off process (panel (e)). Next, the silica layer is etched through the chromium mask by a mixture of CHF3 and O2 gasses (panel (f)), and the chromium mask is removed. The etching defines isolated trenches in the silica layer, with 2 μm depth and 2 μm width (panel (g)). The etched wafers are then diced into samples. At the last stage of the process, a 1 μm-thick As2S3 core is deposited to partially fill the trench patterns, using thermal evaporation (panel (h)). As2S3 is also deposited on the upper surface of un-etched silica regions, outside the trench patterns (see panel (h)). However, the etching depth is sufficient to prevent the coupling of light from waveguide cores into these upper ChG deposits. A protective layer of PMMA is spin-coated on top of the fabricated waveguides. Figure 1 (right) shows a scanning electron microscope cross-sectional image of a waveguide facet (false colors), processed using a focused ion beam. The calculated nonlinear coefficient of the waveguides is 5.9 [Wm]-1. While inverse ridge waveguides of ChG-in-silica were previously fabricated following a similar process [7], their nonlinear optical properties were not examined.
Light was coupled in and out of devices under test using lensed fibers with spot-size diameter of 2 μm (Fig. 2 (left)). The linear propagation losses and the coupling efficiency of the devices were characterized using measurements of end-to-end transmission in waveguides of different lengths. Coupling losses of 6.3 dB per facet and linear propagation losses of 1.25 dB/mm were observed. The high linear losses are primarily due to roughness in the etched silica sidewalls. FWM was characterized by coupling two pump pulses, at wavelengths 𝜆1,2 = 1549.72 nm and 1550.08 nm, into a 4.6 mm-long waveguide. The coupled peak power of each pump pulse at the device input was 26 dBm, and the corresponding average power was 11.3 dBm. Figure 2(right) shows the measured optical power spectral density at the waveguide output. FWM products to the sides of the two pump waves are observed. The FWM efficiency of -40 dB corresponds to a nonlinear propagation coefficient of 6.5±1 [Wm]-1. This value is in good agreement with predictions, and comparable with those of etched As2S3 waveguides [4]. The results establish the proposed method for the fabrication of highly-nonlinear, ChG-in-silica waveguides. Ongoing work addresses the reduction of linear propagation losses, the enhancement of nonlinear propagation through the use of selenium-based ChG compositions, and the characterization of SBS in fabricated devices.
Figure.
Refernces
[1] B. J. Eggleton, B. Luther-Davies, and K. Richardson, "Chalcogenide photonics," Nature Photon. 5(3), 141-148 (2011).
[2] B. J. Eggleton, T. D. Vo, R. Pant, J. Schr, M. D. Pelusi, D. Y. Choi, S. J. Madden, and B. Luther-Davies, “Photonic chip based ultrafast optical processing based on high nonlinearity dispersion engineered chalcogenide waveguides,” Laser Photonics Rev. 6(1), 97–114 (2012).
[3] B. Morrison, A. Casas-Bedoya, G. Ren, K. Vu, Y. Liu, A. Zarifi, T. G. Nguyen, D.-Y. Choi, D. Marpaung, S. J. Madden, A. Mitchell, and B. J. Eggleton, "Compact Brillouin devices through hybrid integration on silicon," Optica 4(8), 847-854 (2017).
[4] M. R. Lamont, B. Luther-Davies, D. Y. Choi, S. J. Madden, and B. J. Eggleton, “Supercontinuum generation in dispersion engineered highly nonlinear (γ = 10 /W/m) As2S3 chalcogenide planar waveguide,” Opt. Express 16(19), 14938–14944 (2008).
[5] S. J. Madden, D. Y. Choi, D. A. Bulla, A. V. Rode, B. Luther-Davies, V.G. Ta’eed, M.D. Pelusi, and B.J. Eggleton, “Long, low loss etched As2S3 chalcogenide waveguides for all-optical signal regeneration” Opt. Express 15(22), 14414–14421, (2007).
[6] C. G. Poulton, R. Pant, and B. J. Eggleton, “Acoustic confinement and stimulated Brillouin scattering in integrated optical waveguides,” J. Opt. Soc. Am. B 30(10), 2657–2664 (2013).
[7] Y. Zhai, R. Qi, C. Yuan, W. Zhang, and Y. Huang, “High-quality chalcogenide glass waveguide fabrication by hot melt smoothing and micro-trench filling,” Appl. Phys. Express 9(5,) 052201 (2016).