Underwater shock wave generation using rapid expansion of an elastic tube connected to a diaphragmless shock tube
Yohei Yamada
Jingzhu Wang
Akihisa Abe
Graduate School of Maritime Sciences, Kobe University
Underwater shock waves have been applied in the fields of mechanical engineering [1], medical treatment [2], food science [3], etc. Generally, an underwater shock wave is generated by any of electric discharge, explosion of explosives, laser-induced bubbles, and fast impingement of a projectile, in which tremendous energies should be instantaneously discharged [4]. Considering development of industrial applications, safety and reduction in cost will be required for underwater shock wave generation. As an ingenious method replacing conventional ones, we propose the use of shock wave generator operated by higher pressure gas. However, because of difference between physical properties of gas and liquid, it is not easy to produce underwater shock waves. Therefore, in order to introduce shock pressure from air to water, some new ideas have to arise.
In the present report, the underwater shock wave generation has been tried using an original diaphragmless shock wave generator. Operation of a rapid opening valve on a diaphragmless shock tube corresponding to rupture on a diaphragm shock tube should be completed within 1 ms. For the improvement of performance, a pre-acceleration section has been designed and a permanent neodymium magnet is installed. Opening time is as much as 30% faster than that without the above assistance, and its minimum value is 0.39 ms at the initial driving pressure of 0.9 MPa. As a result, the diaphragmless shock tube can produce shock waves, Mach number of which is up to 1.6 [5].
Figure 1 shows a schematic diagram of a trial experimental setup. A silicone tube is connected to the exit of the shock tube, and plays a role of an elastic converter. This silicone tube is expanded in the radial direction by discontinuous jump of the pressure at an incident shock wave front, and its external surface compresses ambient water. In visualization experiments, moving shadows considered as pressure waves propagating in water are observed along the tube. However, underwater compression waves are very weak, and any pressure pulses could not be measured.
Also, in order to produce strong pressures that can induce rapid deformation of an elastic material, an axis-symmetric numerical calculation [6] has been carried out. A second-order accurate explicit TVD finite differential scheme of the Harten-Yee type [7] is used in this simulation. Whether the operational pressure can be enhanced by shock wave reflection in an elastic tube or not is numerically investigated. Figure 2 shows the calculation area. The x-axis is the rotational axis. The conditions of boundaries OA and DE are those of inflow and outflow, respectively, and the other boundaries are rigid walls. The boundary CD corresponds to a surface of a silicone tube, however, the elastic deformation of the tube is ignored in the calculation. The nose shapes of the inserted rigid body are flat and conical. Figure 3 shows a comparison of pressure distributions formed by different noses of inserted rigid objects. Figure 3 (a) is in the case of a flat nose, while Fig. 3 (b) is in the case of a conical nose, and tangent of the half vertex angle θ is 1. In Fig. 3 (a), the reflected waves mainly propagate to the upper stream, and their front to the y-direction is weakened by the expansion waves generated at the corner of the inserted object and ‘B’. In Fig. 3 (b), the reflected waves gradually become stronger along an inclined surface and go to the boundary CD. Then higher pressures are locally obtained. The ratios of maximum pressures predicted at CD in Fig. 3 (a) and (b) to the initial incident shock pressure of Mach number 1.5 are 2.0 and 2.3, respectively. Therefore, it is expected that radial expansion of a silicone tube can be remarkably accelerated and underwater shock waves can be generated using a silicone tube.
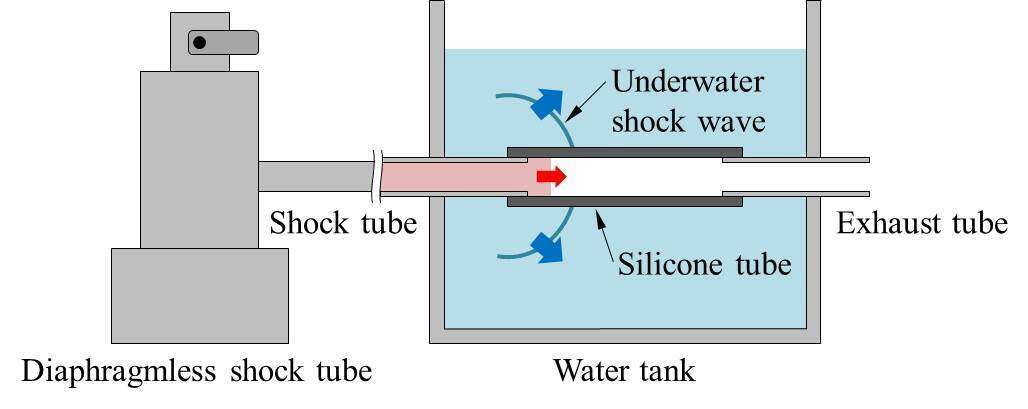
Fig. 1 Schematic diagram of the experimental setup
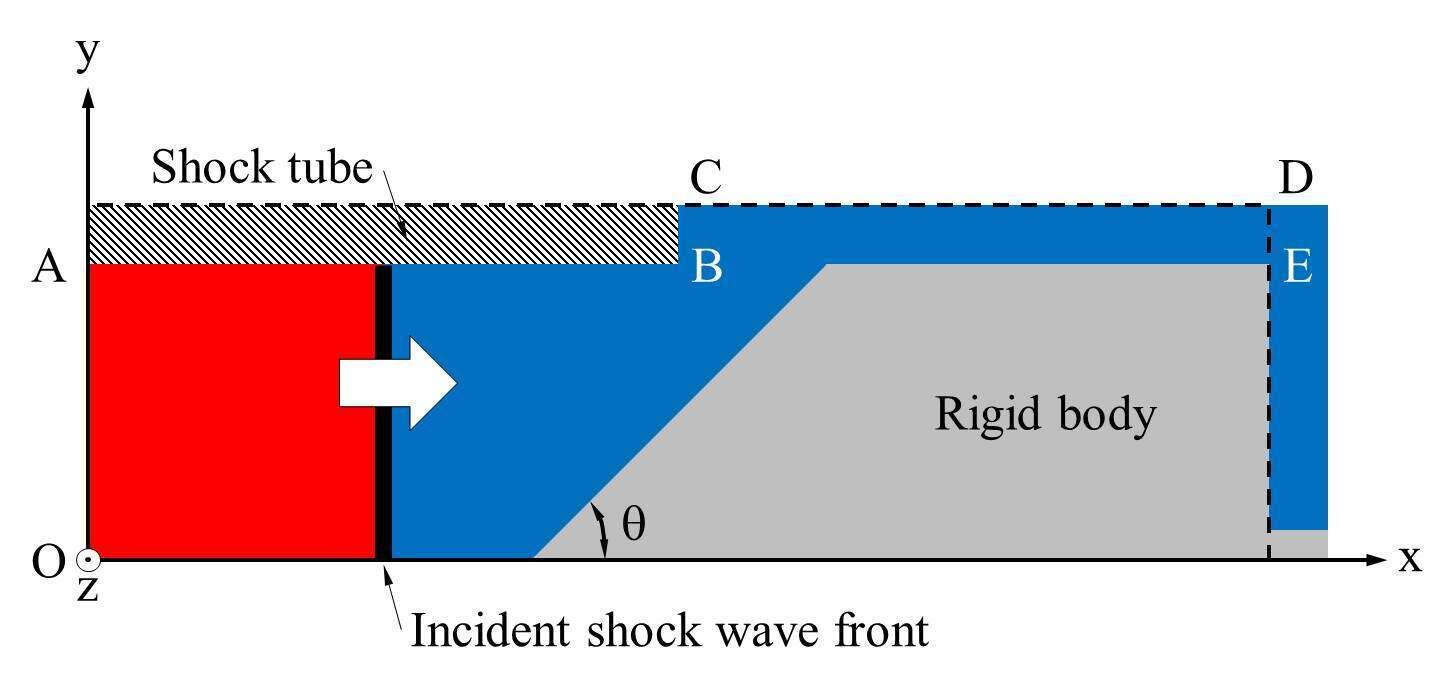
Fig. 2 Illustration of computational area and the initial condition
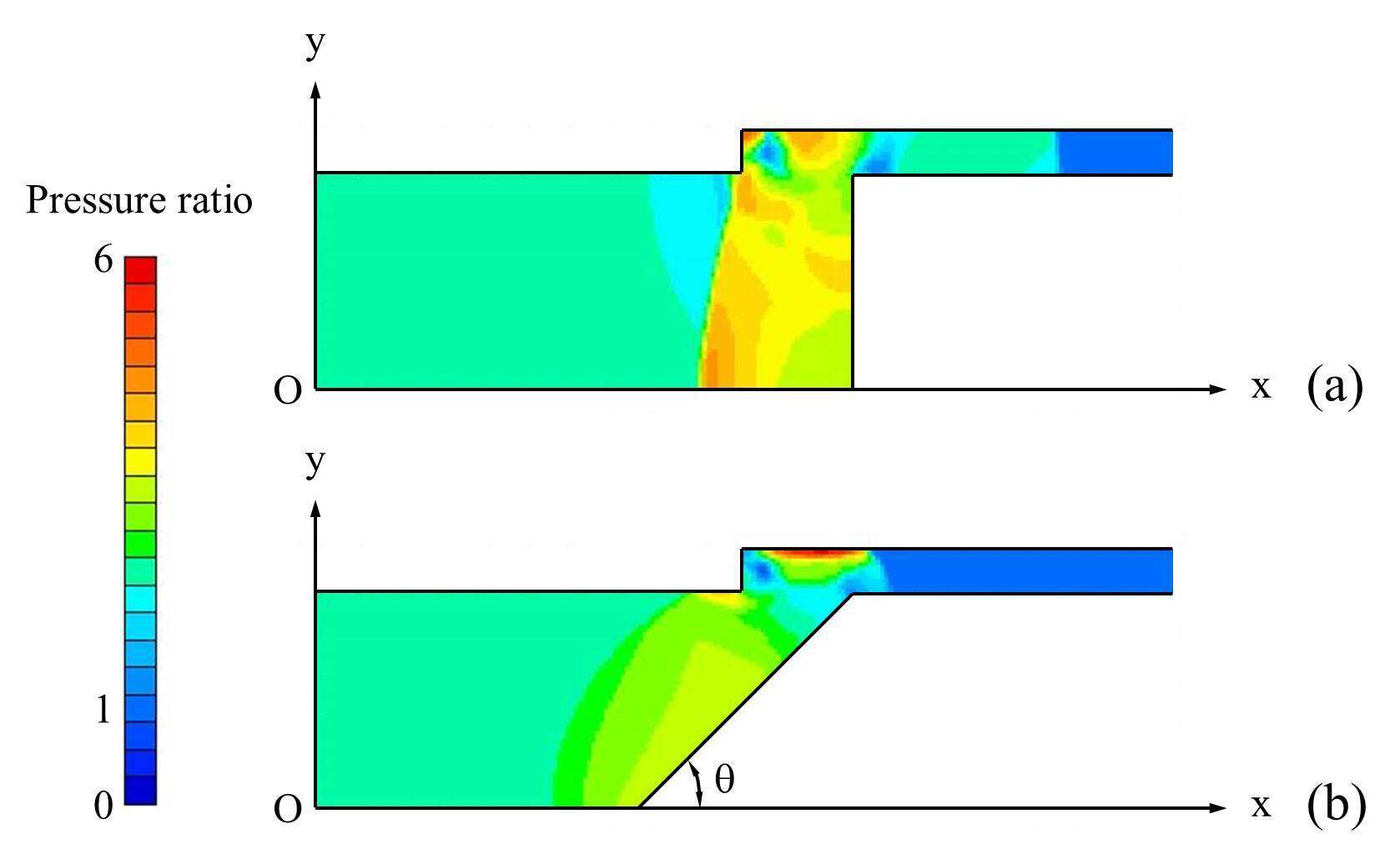
Fig. 3 Comparison of numerical results on pressure distributions; (a) flat nose, and (b) conical nose
References
- Hokamoto, K. and Mori, A., Visualization of high-velocity phenomena under explosion and impulsive pressure assisted by numerical simulation, Journal of the Japan Society for Precision Engineering, Vol.79, No.7 (2013), pp.626-630 (in Japanese).
- Tamagawa, M., Yamanoi, I. and Matsumoto, A., Fundamental investigation for developing drug delivery systems and bioprocess with shock waves and bubbles (Numerical analysis of deformation of cell model and observation of bubble behavior near the cell-membrane model), JSME International Journal Series C Mechanical Systems, Machine Elements and Manufacturing, Vol.44, No.4 (2001), pp.1031-1040.
- Higa, O., Matsubara, R., Higa, K., Miyafuji, Y., Gushi, T., Omine, Y., Naha, K., Shimojima, K., Fukuoka, H., Maehara, H., Tanaka, S., Matsui, T. and Itoh, S., Mechanism of the shock wave generation and energy efficiency by underwater discharge, The International Journal of Multiphysics, Vol.6, No.2 (2012), pp.89-98.
- Takayama, K. ed., Shock Wave Handbook (1995), pp.3-6, Springer-Verlag Tokyo (in Japanese).
- Abe, A., Sugahara, K. and Yamada, Y., Performance evaluation of a diaphragmless shock tube with rapid opening valve assisted by magnetic force, Transactions of the Japan Society of Mechanical Engineers, Series B, Vol.79, No.806 (2013), pp.1973-1984 (in Japanese).
- Meguro, T., Saito, T., Yang, J. and Takayama, K., Numerical simulation of shock wave generation in diaphragmless shock tube, Proceedings of the 7th Computational Fluid Dynamics Symposium (1993), pp.47-50 (in Japanese).
- Yee, H. C., Warming, R. F. and Harten, A., Implicit total variation diminishing (TVD) schemes for steady-state calculations, Journal of Computational Physics, Vol.57, Issue 3 (1985), pp.327-360.
|