Explosive/Blast forming is used for high velocity frictionless forming of thin sheets into complicated shapes which are difficult to form by conventional method [1]. To study the dynamic behaviour of shock loaded material, Stoffel [2] used conventional shock tube to deform plates and characterized macroscopic strain based on mid-point deflection. Authors have also studied the micro structural and texture changes [3-5] in the macrocrystalline material. Recent study by Ray [6] on shock deformed aluminium alloy shows that shock deformed samples shows characteristic texture evolution with high Brass {110} component. A comprehensive review on microstructural issues associated with dynamic deformation such as twins, microbands, grain size effects, shear bands, and dynamic recrystallization by Murr [7] gives insightful information of material behaviour under dynamic loading for face centered cubic and body centered cubic material with different stacking fault energy and grain sizes. However the material behaviour under blast loading has barely been addressed specifically in the nano sized grain regime. The aim of the present work is to understand the deformation mechanism under the high strain rate deformation like shock/blast loading for nanocrystalline nickel and macrocrystalline nickel.
Initial samples with nanocrystalline and macrocrystalline grain size were prepared by different method. Nanocrystalline nickel was prepared by pulsed electrodeposition method whereas Macrocrystalline grain sized nickel was prepared by cold rolling followed by annealing. Nickel was rolled to a final thickness of 0.2 mm. Rolled nickel sheet was then annealed at 400 oC for 1hour to get equiaxed macrocrystalline grains. Pulsed electrodeposition of nickel was carried out in a sulfamate bath. The electrolyte bath contained 150 gpl (gram per litre) of nickel sulfamate, 0.5 gpl of saccharine and 0.1 gpl of sodium lauryl sulphate. Deposition for 12 hours resulted in 0.3 mm thick sheet of nanocrystalline nickel. The deposited nanocrystalline film has fibre texture. Grain size calculated using X-ray diffraction method gives average grain size of 28 nm in the deposited film. Due to limitation in the size of nanocrystalline film that can be obtained via pulsed electrodeposition method and to compare the behaviour of macrocrystalline and nanocrystalline nickel, nickel discs of diameter 12 mm and thickness 0.2 mm were used for the present study.
Nickel discs were deformed using Nonel tube, which can produce highly repeatable blast wave. The deformation phenomenon has been studied by observing the changes in microstructure and micro-texture as a result of blast loading. Electron back scattered diffraction technique is used to study the microstructure and micro-texture changes for macrocrystalline nickel. Pole figure, Inverse pole figure and orientation distribution function obtained from electron backscattered diffraction data give insight of the micro-mechanism of deformation. For nanocrystalline nickel, the deformed samples are studied under transmission electron microscope due to the limitation of step size in scanning electron microscope used for electron backscattered diffraction study.
Fig. 1 shows the deformed macrocrystalline nickel disc cut transversally along the rolling direction. Electron back scattered diffraction scans were done at centre region where the displacement was maximum in the disc as representative of deformed region and at the corner of disc as representative of undeformed region. Fig. 2 shows the inverse pole figure map for undeformed and deformed region of macrocrystalline nickel. The triangular coloured figure maps the colour in the inverse pole figure to the corresponding crystal orientation at that point. It can be seen in Fig. 2 that after deformation the crystals are reorienting to (100) and (112) orientation. As the grains are very few along the thickness directions in macrocrystalline nickel sample, comment on macrotexture of sample after deformation will not statistically correct. Further analysis is to be done.
The transmission electron microscopic analysis of nanocrystalline nickel is to be done.
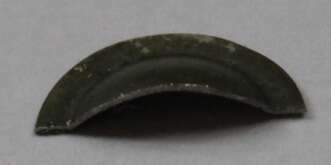
Fig. 1 Cross section of Ni disc deformed using Nonel tube
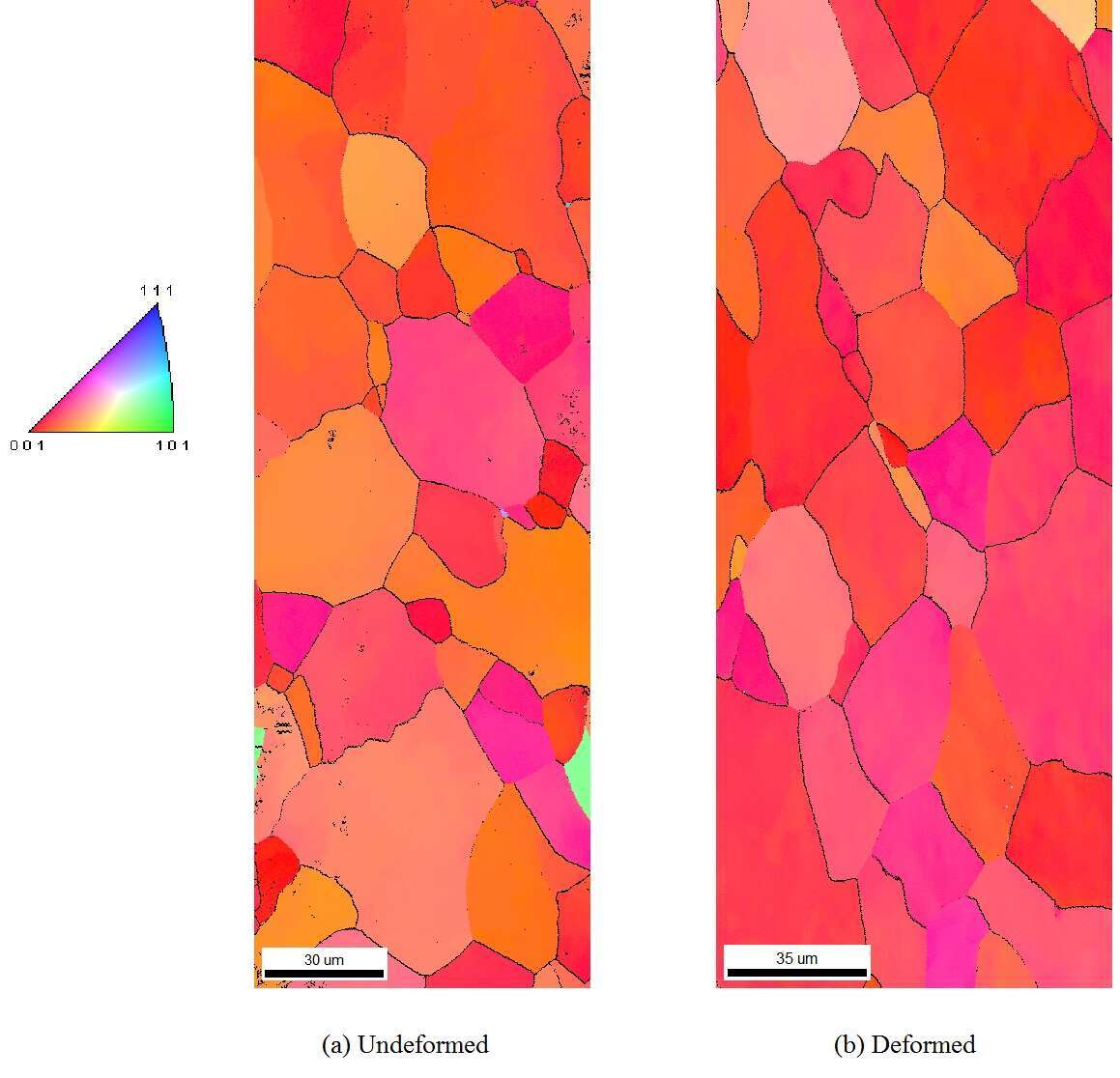
Fig. 2 Inverse Pole Figure maps from EBSD for a) underformed region and b) deformed mid point (maximum displacement) region of macrocrystalline nickel.
References
[1] S.F. Golovashchenko, N.M. Bessonov, A.M. Ilinich, Journal of Materials Processing Technology 211 (2011) 875.
[2] M. Stoffel, Mechanics Research Communications 33 (2006) 775.
[3] R.J. De Angelis, J.B. Cohen, Transactions of American Society for Metals 58 (1965) 700.
[4] L.F. Trueb, Journal of Applied Physics 40 (1969) 2976.
[5] M.F. Rose, T.L. Berger, Philosophical Magazine 17 (1968) 1121.
[6] Nachiketa Ray, Gopalan Jagadeesh, Satyam Suwas, Materials Science and Engineering A (2014), In press.
[7] Murr, Lawrence E., and E. V. Esquivel, Journal of materials science 39.4 (2004): 1153-1168.