I. Introduction
The separation of boundary layer is one of the most unwanted phenomena in high speed aerodynamics [1, 2]. A common active flow control method to suppress separation is by removing the low momentum fluid near to the wall. This is achieved through bleed holes provided at the wall, which require great amount of energy [3]. This calls for passive methods of flow control like passive cavity, vortex generators, micro porous plate, mesoflaps, vanes, etc. [4, 5, 6]. Among these, vortex generators are the most widely used passive methods to decrease boundary layer losses.
Fig. 1 shows the trend in ramp based MVGs for controlling shock induced separation. The main objective of this study is to demonstrate a combined passive flow control system consisting of micro ramps and passive injection through ramps. This method can be considered passive if one can utilize the injection air from the free stream of the aircraft itself, and the injection pressure is less than the total pressure.

Figure 1 Recent trends in ramp based MVGs. (a) micro ramp. (b) split-ramp [7]. (c) ramped-vane [8]. (d) slotted-ramp [9]
II. Results
Experiments were conducted with MVGs according to the optimized data given by Anderson et al. [10]. There were 3 MVGs in a row, with M = 1.3 at the start of the MVGs. A normal shock of strength M=1.5 was standing down steam of the MVGs. The top wall of tunnel has a divergence of 40 which helps in stabilizing the normal shock. Fig. 2 shows horizontal knife edge schlieren pictures where the bottom boundary layer appears as white in color at the micro ramp side. The flow is from left to right. There is a weak oblique shock (WOS) coming from tunnel floor and its effect can be neglected. Consider the two cases described below.
Case (a): Micro ramps without injection.
Fig. 2a shows the schlieren images taken for MVGs without injection. It is evident that the micro ramp induces two oblique shocks, one from its leading edge (LES) and other from the trailing edge (TES). There exists a low momentum and a high momentum region in the wake of micro ramps [11, 12]. The trailing edge shock is due to the up wash effect created by the primary vortices generated from the MVG. This results in a thickened boundary layer just downstream of the MVG as seen from figure 2a. There exist This intermediate low momentum region makes the conventional micro ramps unfit for complete separation control.
Case (b): Micro ramps with injection.
When injection takes place through the trailing edge, the trailing edge oblique shock is replaced with a weak compression wave as shown in figure 2b. The boundary layer downstream to this MVG is thinner compared to the conventional MVG (case (a)). This indicates that due to the injection, there exists a high momentum region downstream of the trailing edge. Therefore a much fuller boundary layer exists downstream of this strategy.
This suggests that injection through micro ramps has promise in decreasing the boundary layer separation. The full paper will contain results from schlieren imaging, oil flow visualization, and pressure measurements.
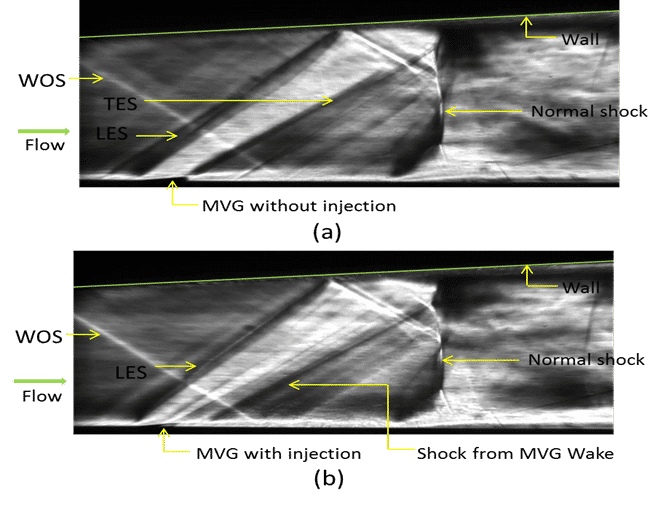
Figure 2. Schlieren images for both cases with a normal shock also. (a) Micro ramps without injection (b) Micro ramps with injection.
References
[1] Babinsky, H., Harvey, J. K., “Shock Wave-Boundary-Layer Interactions”, Cambridge University Press (2011).
[2] Seddon, J., and Goldsmith, E. L., “Intake Aerodynamics,” 2nd ed., Blackwell Science, Boston, 1999.
[3] Fukuda, M. K., Hingst, W. G., and Reshotko, E., “Control of Shock Wave-Boundary Layer Interactions by bleed in supersonic mixed compression inlets,” NASA CR-2595, Aug. 1975.
[4] McCormick, D. C., “Shock/Boundary-Layer Interaction Control with Vortex Generators and Passive Cavity,” AIAA Journal, Vol. 31, No. 1, Jan. 1993, pp. 91–96.
[5] Srinivasan, K. R., Loth, E., and Dutton, C. J., “Aerodynamics of Recirculating Flow Control De-vices for Normal Shock/Boundary-Layer Interactions”, AIAA Journal, Vol. 44, No. 4 (2006), pp. 751-763.
[6] Ashill, P. R., Fulker, J. L., Hackett, K. C., “Research at DERA on sub boundary layer vortex generators (SBVGs)”, AIAA Paper 2001-0887, 39th AIAA Aerospace Science Meeting and Exhibit, Reno, NV, January 8–11, 2001.
[7] Lee, S., Loth, E., and Babinsky, H., “Normal Shock Boundary LayerControl with Various Vortex Generator Geometries”, 5th Flow Control Conference, Chicago, AIAA Paper 2010-4254, Jun–Jul 2010.
[8] Rybalko, M., Babinsky, H., and Loth, E., “Vortex Generators for a Normal Shock/Boundary-Layer Interaction with a DownstreamDiffuser,” Journal of Propulsion and Power, Vol. 28, No. 1, 2012, pp. 71–82.
[9] Sharma, P., and Ghosh, S., “A Novel Vortex Generator for Mitigation of Shock-Induced Separation,” 52nd Aerospace Sciences Meeting, 2014.
[10] Anderson, B., Tinapple, J., and Surber, L., “Optimal Control of Shock Wave Turbulent Boundary Layer Interactions Using Micro-Array Actuation,” AIAA Fluids Engineering Conference, AIAA Paper 2006- 3197, June 2006
[11] Babinsky, H., Li, Y., and Pitt Ford, C. W., “Micro-ramp Control of Supersonic Oblique Shock Wave/Boundary-Layer Interactions,” AIAA Journal, Vol. 47, No. 3, March 2009, pp. 668–675.
[12] Xiao Wang, X., Yan, Y., Sun, Z., Liu, C., “The Vortical Structures in the Rear Separation and Wake Produced by a Supersonic Micro-Ramp,” Flow Turbulence Combust (2014) 93:25–36.
[13] Blinde, P. L., Humble, R. A., Van Oudheusden, B. W., and Scarano, F., “Effects of micro-ramps on shock wave/turbulent boundary layer interaction,” Shock Waves (2009) 19:507–520.
[14] Bo, W., Weidong, L., Yuxin, Z., Xiaoqiang, F and Chao, W., “Experimental investigation of the micro-ramp based shock wave and turbulent boundary layer interaction control,” Phys. Fluids 24, 055110 (2012).
[15] Giepman, R. H. M., Schrijer, F. F. J., and van Oudheusden, B. W., “Flow control of an oblique shock wave reflection with micro-ramp vortex generators: Effects of location and size,” Phys. Fluids 26, 066101 (2014).