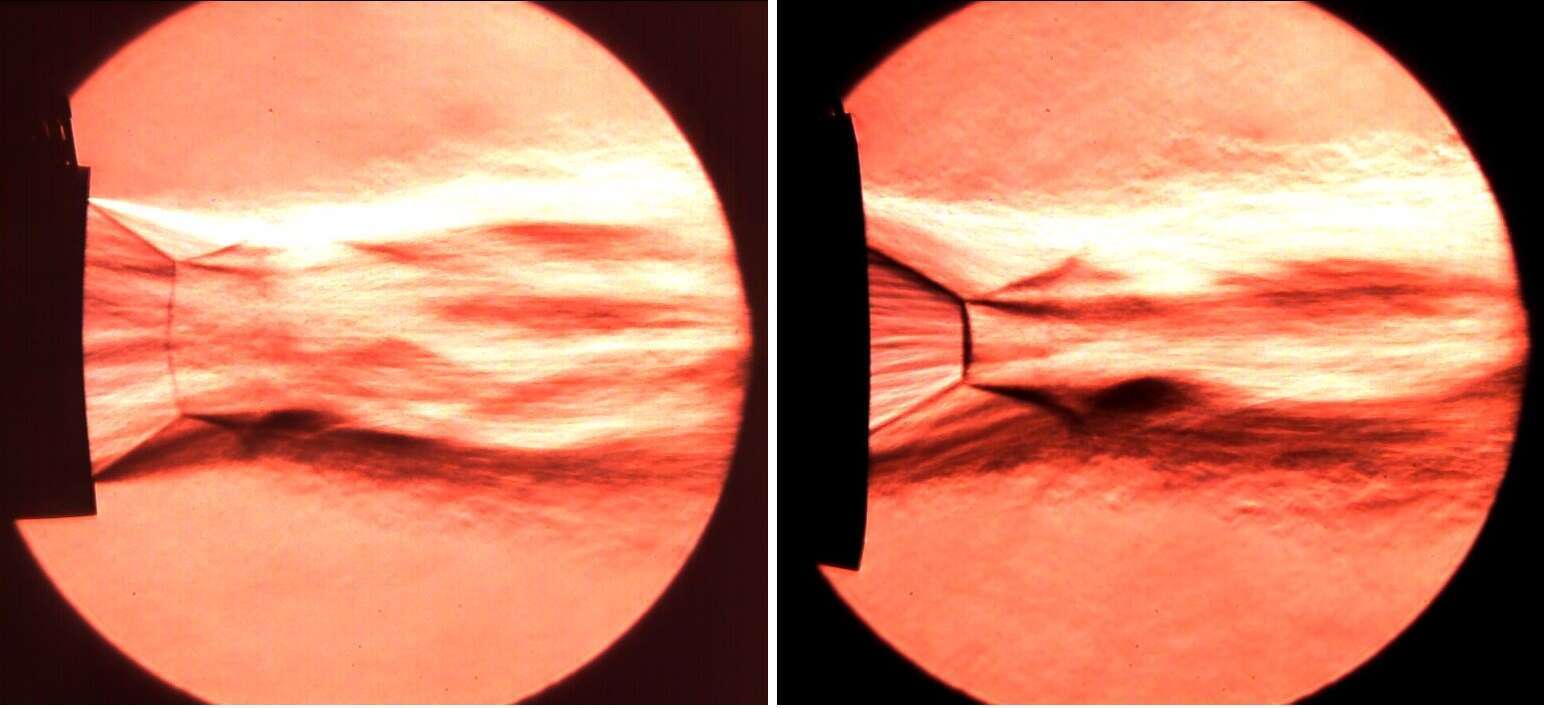
Flow fluctuations in or around rocket nozzles can lead to a deformation of their structure. In the case of separated nozzle flow, the flow structure interaction is a self-reinforcing effect, which can potentially lead to structural damages. In order to understand and study this phenomenon, a collaborative work between the institutes of Space propulsion and Aerodynamics and flow technology of the German Aerospace Center (DLR) has been started in the framework of project ProTAU. A step by step, both numerical and experimental investigation is carried out on nozzle ovalization.
The study started with the validation of the numerical method to simulate separated flow in axisymmetric cold flow sub-scale conventional nozzles. Based on three initial non-deformed nozzles, seven different out-of-round geometries have been defined. The parameters of interest were the amplitude of the deformation, the position at which it starts and the axial evolution of the deformation. The initial nozzles feature different design Mach number and hence wall angle. The seven deformed nozzles were numerically simulated. Three geometries were selected out of them for experimental investigation, after the simulation had shown the measurability of the flow behavior within the facility capability.
The tests were conducted at DLR Lampoldshausen test facility P6.2. Dry nitrogen was used as feeding cold flow gas with total pressure up to 6 MPa. The nozzle was mounted on the horizontal rig and tests were conducted under ambient conditions. The feeding pressure was progressively varied with a constant gradient, leading to the displacement of the separation point along the nozzle contour until full flowing condition. Wall pressure ports placed within small axial intervals permit to follow the position of the separation point. As the nozzle deformation leads to a circumferential deformation of the separation line the wall pressure ports were distributed in five rows. The first line was placed along the major axis and the fifth on the minor axis. The lines were regularly distributed with an angle of 22.5°. Each line features nineteen positions, for a total of 95 wall pressure ports for each nozzle. In addition to the pressure measurement, a schlieren optics was implemented. The shock system exiting the nozzle has been recorded with a black and white schlieren installation and a high speed camera. In order to capture the 3-dimensional shape of the shock system, each nozzle was progressively turned around its axis. The pictures obtained were then processed using a Matlab code. The position and shape of the shock system has been extracted out of the schlieren pictures. The figure illustrates the shock system in the same ovalized nozzle at the same test conditions in the major and minor axis views.