The primitive concept of resistojet thruster has been developed with simplicity of heating inert gas and economic feasibility for the propulsion of small space vehicles since the early stage of space development [1]. Besides its engineering excellence, the requirement for the environment problems persuades us to use an alternative against chemical pollution at the low-altitude orbit near the earth. However, the power efficiency of resistojet is no better than other kinds of propulsive methods: for example, the specific impulse is 48 s for the driver gas of Xe in the commercial products. To improve this, the operating temperature should be increased, but the surface radiation to the background universe makes it difficult.
In the preliminary research [2], the complicated micro-scale shock wave structure is studied in the region of under-expanded jet: Fig. 1. A model of the axisymmetrically feeding thermal expansion part is proposed for this study: Fig. 2 where the change of geometry as well as several key parameters was investigated with multiple physics models for the optimization of output performance. Additionally, the nozzle shape is designed to maximize the specific impulse that is a ratio between the thrust force and the mass flow rate of driver gas under the consideration of viscous and thermal boundary layer: Fig. 3.
[1] Electric Propulsion article in Encyclopedia of Physical Science and Technology, 3rd Edition, Academic Press, San Diego, v.5, pp. 125-141, 2002.
[2] Kim, S.S., Chang, S.M., “Compressibility Effect in the Axisymmetric Internal Flow Past a Microgap,” Transactions of KSME(B), 34(12): 1061-1069, 2010.
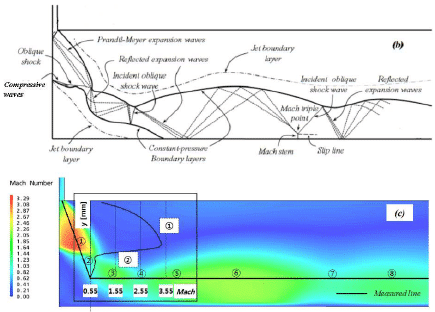
Fig. 1 Complex shock structure in the axisymmetric under-expanded jet model.
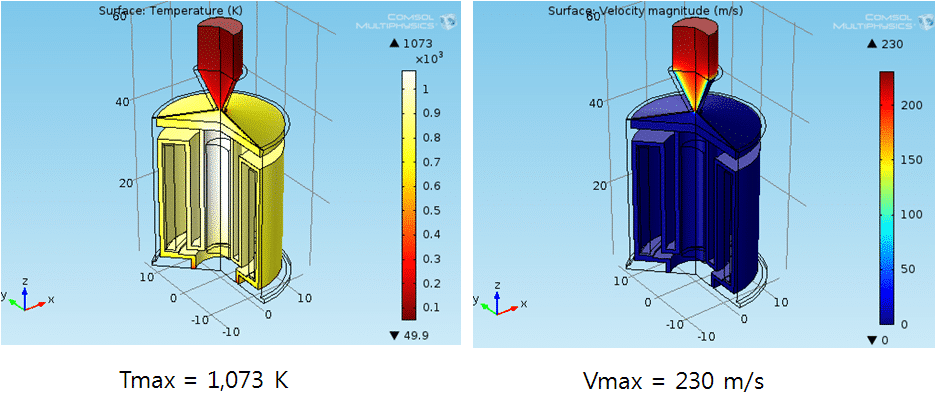
Fig. 2 The axisymmetric model for resistojet thruster driven with Xe: (left) temperature, and (right) flow velocity.

Fig. 3 The nozzle shape designed for the optimization of specific impulse.