The transverse injection in a supersonic cross-flow is a problematic which can be encountered in several aerodynamic applications such as fuel injection in scramjet combustor, missile control, drag reduction and thrust vector control. In recent years, an extended analytical, numerical and experimental work has been carried out by the authors [1,2] to investigate vectoring performances of a supersonic axisymmetric nozzle using secondary fluid injection. The experiments were conducted in the hypersonic test facility EDITH of the CNRS institute ICARE in Orléans, France. In this context, the present study focuses on the secondary injectant gas thermodynamic properties influence on the vectoring performance of a supersonic nozzle. For this purpose, performance aspects of fluidic thrust vectoring concept have been experimentally investigated on a truncated ideal contour (TIC) nozzle model using a variety of gas species (with low to moderate molar mass) as injectant. Qualitative and quantitative diagnostics consisted of Z-schlieren visualization, 3-axis force balance and static and dynamic parietal pressure measurements. The experimental results are compared to the numerical and analytical findings.
Figure 1 shows the experimental facility used in this investigation. It consists of a high pressure air supplying line to the main nozzle inlet. The supersonic TIC nozzle is placed inside a test chamber connected to two powerful vacuum pumps maintaining the desired exit ambient pressure. The injectant gas is supplied from the secondary high pressure tank with separated regulator.
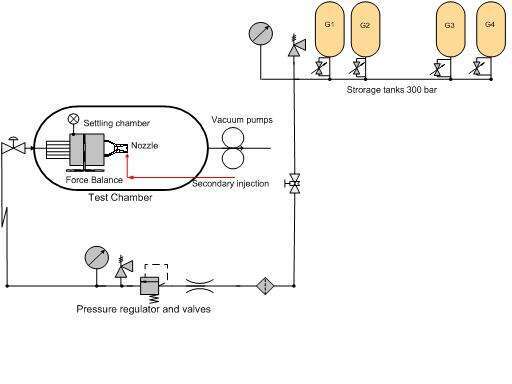
Figure 1. Scheme of the experimental setup
The gas properties and injection conditions are listed in table 1.
The investigation was conducted testing four injectant gas species of different molar mass (Air, He, CO2, Ar) on two major injection condition sets; setting the constant secondary injection pressure ratio SPR for all species and by setting the constant secondary to the main flow mass flow rates fm.
Tables 2 and 3 show respectively the vectoring performances in term of thrust deviation angle d for different injectant/main flow gas couples and for different secondary injection conditions. From these results, it’s evident that it’s possible to achieve ameliorated vectoring performance for the same pressure ratio with smaller mass flow rate as is the case of a lighter gas as helium comparing to the more inert gas species. In the other words, one can achieve a far better deviation angle with the same mass flow rate using helium as injectant.
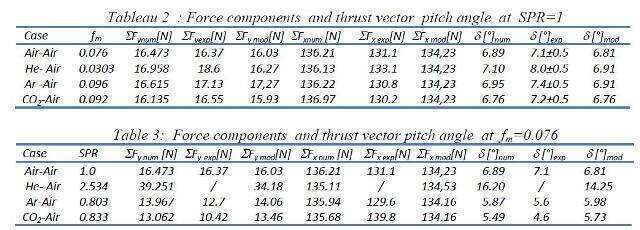
As a consequence, the mass of injecant gas required for the launcher controlling task can be divided by a factor of two or more depending on the molar mass of the gas.
This trend is also depicted in Fig. 2 which shows comparison between numerical, analytical and experimental approaches for the thrust vectoring angle evolution versus the ratio of injectant to the main flow gas product of gas molar mass and specific heats ratio. It’s well known that this parameter plays a dominant role in the jet penetration phenomenon. The comparison between numerical, analytical and experimental methods shows the same trend and give close results considering error margin in all these triple approaches.
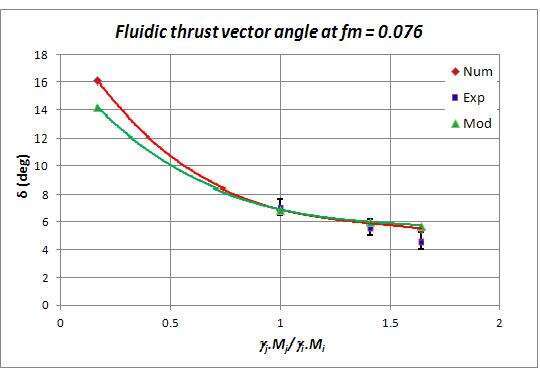
The final paper will contain more detailed analysis of the results and further comparison with numerical and analytical models will be given.
References
[1] Sellam M., Chpoun A., Zmijanovic V., Lago V. 2011. Fluidic thrust vectoring of an axisymmetric nozzle: An analytical model, International Journal of Aerodynamics.
[2] Zmijanovic V., Lago V., Sellam M., Chpoun A., Thrust shock vector control of an axisymmetric conical nozzle via transverse gas injection. Shock Waves J. 24(1) pp 97-111, 2014.