There has been recent global resurgence in the field of hypersonics research. In order to sustain these research efforts it is essential to provide appropriate training to the students at college level. Currently existing experimental facilities used to study hypersonic flows are large in size and the cost to build and maintain them is very high and hence they are not useful as teaching tools. To overcome this, we have successfully developed a hand operated table top hypersonic shock tunnel based on the recently developed Reddy tube [1,2]. This facility is small in size, low in cost and also risk free. Thus, it has enormous potential for the facility to be used for demonstrative undergraduate level experiments on hypersonic flow.
The table top hypersonic shock tunnel is made out of grade SS 304 steel tube and provided with windows to facilitate flow visualization. The viewing windows have diameter of 120 mm. The shock tube has a driver section length of 400 mm and driven section length of 600 mm. A convergent-divergent Mach 6 conical nozzle is connected to the end of the shock tube. The shock tube inner diameter is 31 mm. The exit diameter of nozzle is 78mm and has a throat diameter of 10 mm with a 10 degree angle of divergence. The dump tank inner diameter is 356 mm and has a length of 440 mm with an elliptical door for better cushioning. The test section has provision to mount a model at different positions and angles. Schematic diagram and photograph of the Reddy tube driven table top hypersonic shock tunnel is shown in Fig. 1.
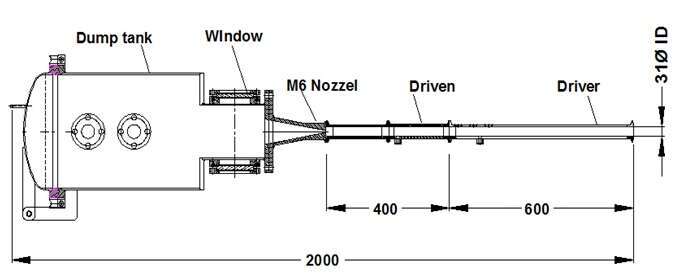
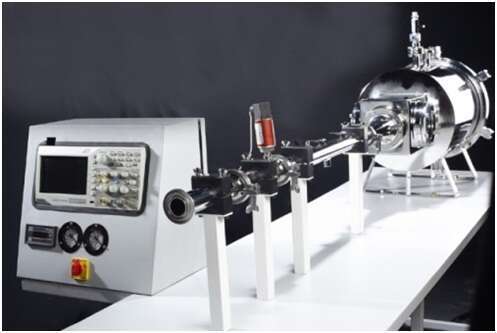
A paper diaphragm (~40 microns thick) between driver and driven sections is used to drive the shock tube. A thinner paper diaphragm is placed between driven section and the nozzle. Vacuum of less than 1 mm Hg is created in the dump tank using a rotary pump. The driver section is pressurized by a plunger that compresses the gas between piston face and the paper diaphragm. When the paper diaphragm bursts, a shock wave is generated in the driven section of the shock tube and the shock tunnel is operated similar to conventional pressure driven shock tunnel. The freestream flow through the test section of the hand operated table top hypersonic shock tunnel has been calibrated using pitot pressure measurements and it is found that the flow Mach number is very close to the nozzle design Mach number of 6. We have also carried out measurement of stagnation point heat transfer rate for a hemispherical model using platinum thin film sensor. The measured value is found to be matching well with the theoretically estimated value using Fay and Riddell equation. Currently experiments to measure drag force on simple body configuration using accelerometer balance system and visualization of hypersonic flow over spherical body using schilieren technique are being carried out. This facility is already being used for teaching hypersonics course in few colleges in India. Detailed results along with other features of the Reddy tube driven table top hypersonic shock tunnel will be presented in the full length paper.
References
- Reddy, K. P. J., In 28th International Symposium on Shock Waves (eds Kontis, K. et al.), Manchester, UK, (2011).
- Reddy K.P.J and Sharath N, “Manually operated piston driven shock tube”, Sci., 104, pp 172-176 (2011).
- Surana K. S, Reddy K. P. J, Joy A. D and Reddy J. N, “Riemann Shock Tube: Evolution, Propagation, Reflection, and Interactions of 1D Normal Shocks in Air; Numerical Simulations and Experiments”, J. CFD, pp. 1-21 (2014).