Rapid mixing and spreading of supersonic jets are two important characteristics in supersonic ejectors, noise reduction in jets and fuel mixing in supersonic combustion. It helps in changing the acoustic and thermal signature in supersonic exhaust. The supersonic nozzles in most cases result in compressible mixing layers. The subsonic nozzles form incompressible mixing layers but at high Mach numbers even they give compressible mixing layers. Jet flow from supersonic nozzles have slower spreading rates compared to subsonic nozzles because rate of growth of compressible mixing layers decreases with increase in Mach number [1].
Many nozzles with exotic shapes have been developed to obtain mixing enhancements in supersonic jets [2]. To achieve enhanced mixing an innovative nozzle named as the Elliptic Sharp Tipped Shallow (ESTS) lobed nozzle has been developed in L.H.S.R., I.I.Sc., India[3]. This nozzle has a unique geometry involving elliptical lobes and sharp tips . These lobes are generated using a simple manufacturing process from the throat to the exit. This lobed and sharp tipped structure introduces streamwise vortices and azimuthal velocity components which must help in enhanced mixing and spreading. The ESTS lobed nozzle has shown mixing enhancement with 4 lobes. The spreading rate was found to be double of the reference conical nozzle [4]. This paper is motivated by the need to investigate the flow physics involved in the ESTS lobed nozzle. The effect of varying ‘the number of lobes’ and ‘the design Mach number’ of the nozzle on the mixing and spreading characteristics will be further discussed.
Figure 1 shows instantaneous images taken at an axial plane with the reference conical and ESTS nozzles with three, four, five and six lobes. The three and four lobed nozzles are for design Mach number 2.0 while the five and six lobed nozzles are for design Mach number 2.5. The stagnation chamber pressure was maintained at 6 bar. An NdYAG laser of 532 nm was used as the light source. The visualization technique used to obtain the images is scattering of a laser sheet by condensed moisture [5]. The low temperature primary flow coming in contact with the moist ambient air results in the condensation of moisture. This condensed moisture is carried by the flow and causes scattering of the laser. This helps in the visualization of the mixing layer.
A comparison of the images of the reference conical nozzle and the ESTS lobed nozzles shows changes in the mixing layers due to the ESTS lobed nozzles. The image of the reference conical nozzle shows a distinct potential core and mixing layers all along. For the ESTS lobed nozzles this distinction becomes unclear shortly after the nozzle exit. Thus mixing of the primary flow and ambient air is enhanced in the case of all the ESTS lobed nozzles. In case of odd numbers of lobes the crest of a lobe is diametrically opposite to the tip of another lobe. Thus the image of the three lobed nozzle shows the mixing layer from the lobe tip, above and the mixing layer from the lobe crest, below. This image shows that the visual thickness of the mixing layer from the lobe crest has a higher growth rate than the mixing layer from the lobe tip. In the case of even numbers of lobes a lobe tip is diametrically opposite to another lobe tip. Thus the mixing layers at any longitudinal position appear geometrically similar on both sides, as in the image of the four lobed nozzle. The images of the five and six lobed nozzles also show some additional structures between the two extreme shear layers that are not seen in the images of the three and four lobed nozzles. Investigations to ascertain the three dimensional nature of the flow are being carried out.
The final paper will discuss the effect of various design parameters on the mixing enhancement due to the ESTS lobed nozzle.
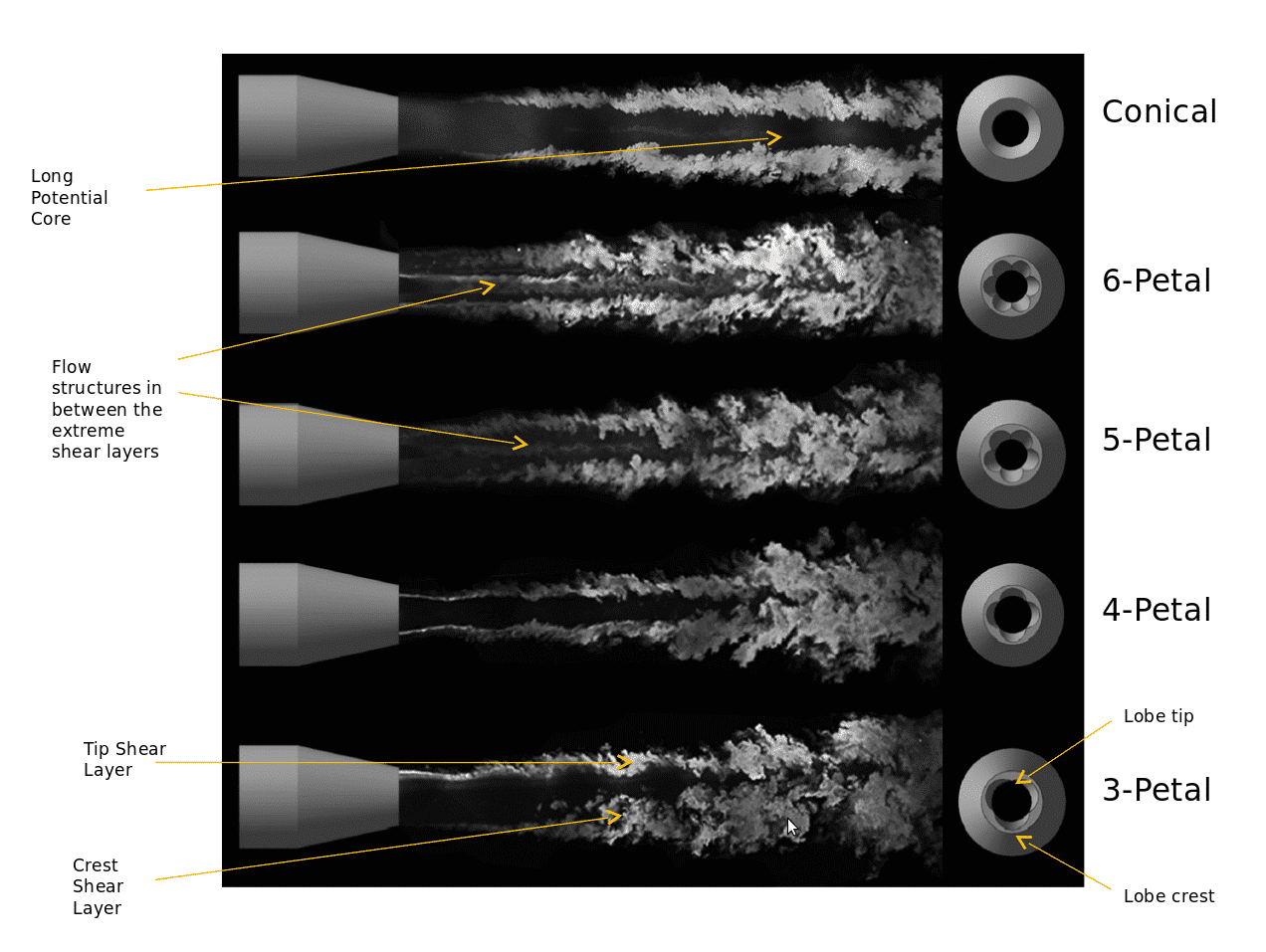
Figure 1: Planar laser scattering images
REFERENCES
1. D. Papamoschou and A. Roshko, "The compressible turbulent shear layer: an experimental study," Journal of Fluid Mechanics, vol. 197, pp. 453477, 1988.
2. E. Gutmark, K. Schadow and K. Yu, "Mixing enhancement in supersonic free shear flows," Annual Review Fluid Mechanics, vol. 27, pp. 375417, 1995.
3. S. Rao, "Experimental investigations on supersonic ejectors," PhD Thesis, Aerospace Engineering, Indian Institute of Science, Bangalore, 2013.
4. S. Rao and G. Jagadeesh, "Novel supersonic nozzles for mixing enhancement in supersonic ejectors," Applied Thermal Engineering, vol. 71, no. 1, pp. 6271, 2014.
5. N. Clemens and M. Mungal, "A planar mie scattering technique for visualizing supersonic mixing flows," Experiments in Fluids, vol. 11, no. 1, pp. 175185, 1991.