Interaction of a blast wave with a structure is a coupled process that involves both gas dynamics and structural dynamics. As carrying out a full scale blast test is difficult, shock tubes are popular devices that are used to simulate such an event as they are capable of generating precise planar shock fronts in a repeatable fashion [1]. Before a shock tube can be used to study such phenomenon, its capabilities in simulating such an event need to be identified. To incorporate the appropriate scaling laws, the pressure needs to be matched and the impulse value has to be scaled down by the ratio of the model lengths [2]. For a quasi static loading, the loading pulse`s pressure is the sole criterion in determining the response of the structure. But for the other dynamic and impulse loading, impulse is also important. For the impulsive event, the pressure is irrelevant and the impulse value of the blast is the only controlling factor. If these two events need to be simulated in the shock wave, special attention has to be paid to the time duration (which is related to the impulse) of the loading pulse.
We are currently in the process of identifying the parameters that would best suit the simulation of a blast test in a shock tube. Experiments and numerical simulations are currently underway to help finalize these parameters. A new vertical shock tube facility that been designed and developed to carry out blast loading studies was used in the current set of experiments (Figure 1). This facility has the provision to vary the lengths of the driver section (3 tubes of 0.5 m each) and the driven section (one tube of 1.5 m, 3 tubes of 0.6m, 1 tube of 0.5 m, and one tube of 0.39 m). The shock tube opens into a test chamber where tests on bigger models such as scaled bunkers, armoured vehicles etc may be tested. A vertical facility was chosen as it would be easier to launch a piston onto a water interface to achieve higher pressures. The focus of the current study however, is on air shocks.
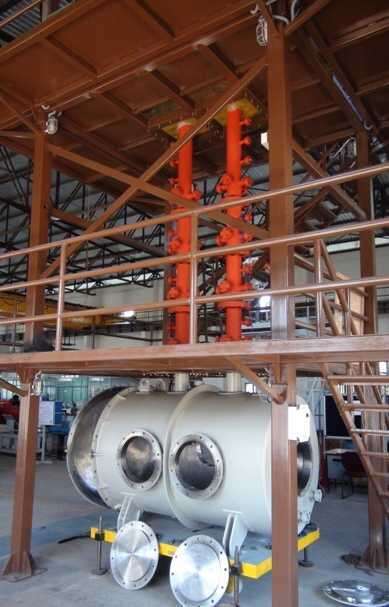
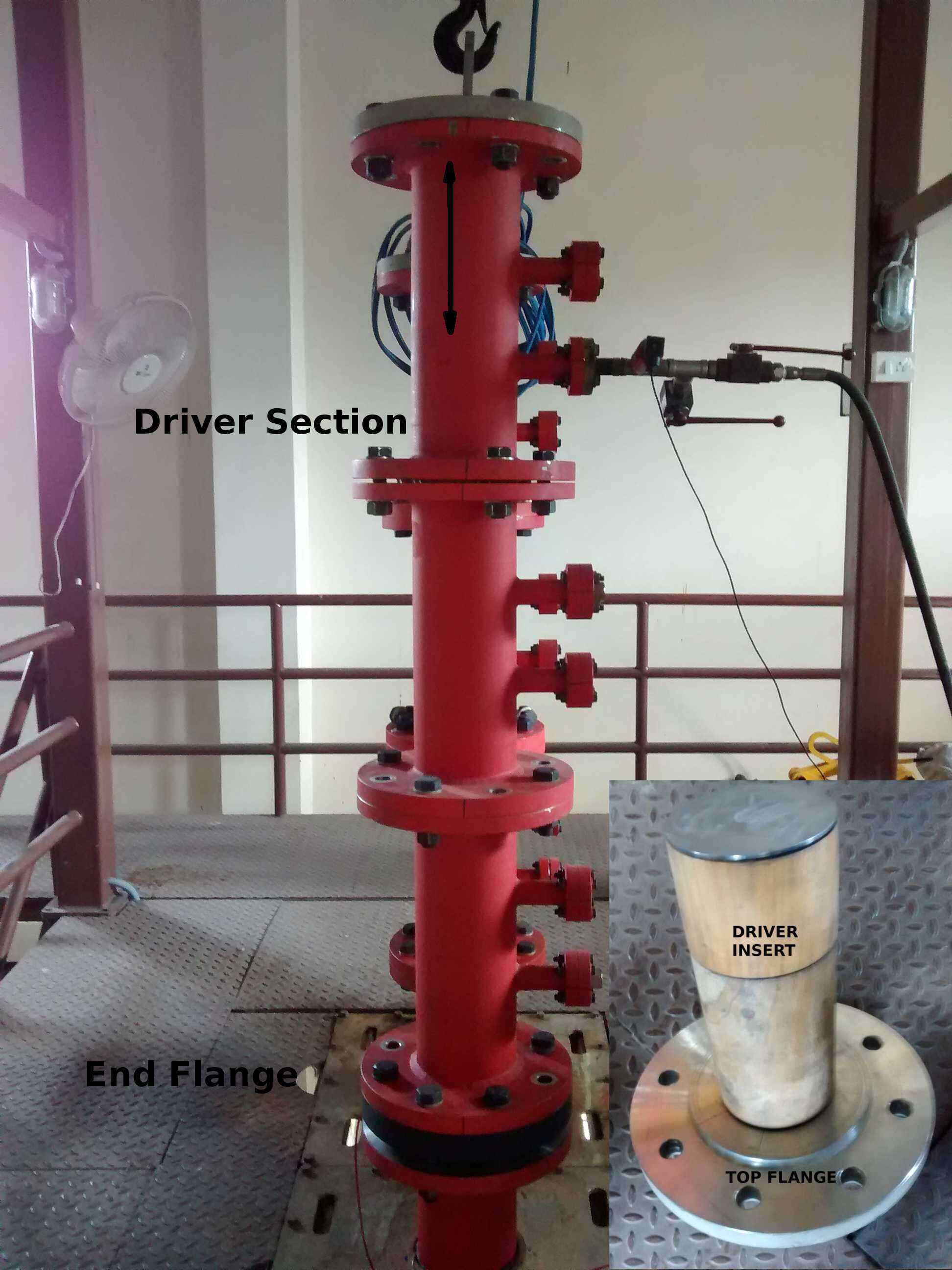
Figure 1: A photograph of the facility Figure 2: Reduced lengths that were to used for a specific condition
Since a blast wave is required at the end wall of the tube, we need to ensure that the expansion fan catches up with the shock front as soon as possible. A simple calculation was done to get an idea on the shortest pulse time that may be achieved in a shock tube. One constraint that was used was that the expansion fan needs to catch up with the shock only after the shock has fully formed. Based on some simplifying assumptions, the total time taken for the expansion fan to catch up with the shock front has been estimated at 1.2 ms. This is an indication of the smallest pulse that can be obtained on a shock tube.
In addition, for reasons that shall be detailed in the full paper, we need to look for a condition where the tail of the expansion fan is stationary. Table shows the conditions where this is achieved using helium as driver gas
P4 (bar)
|
P1 (mm Hg)
|
T4 (K)
|
T1(K)
|
P5 (bar)
|
td (ms)
|
38
|
690
|
300
|
300
|
45
|
1.3
|
53
|
690
|
400
|
300
|
69
|
1.1
|
70
|
690
|
600
|
300
|
100
|
0.8
|
Table 1: Conditions that were found to be best for the shock tube to obtain small pulse duration
The values in the last two columns were computed for a 0.2 m long driver section and for a driven section of 1 m using Fluent. Using the TNT calculator available online [3], this is equivalent to a 80 kg TNT explosion at 4.45 m radius. The first condition was experimentally validated (Figure 2). An insert was used in the driver to reduce its length (Inset of figure 3). This had fallen off and so the signal had got disturbed.
Figure 3: A typical pressure profile at end wall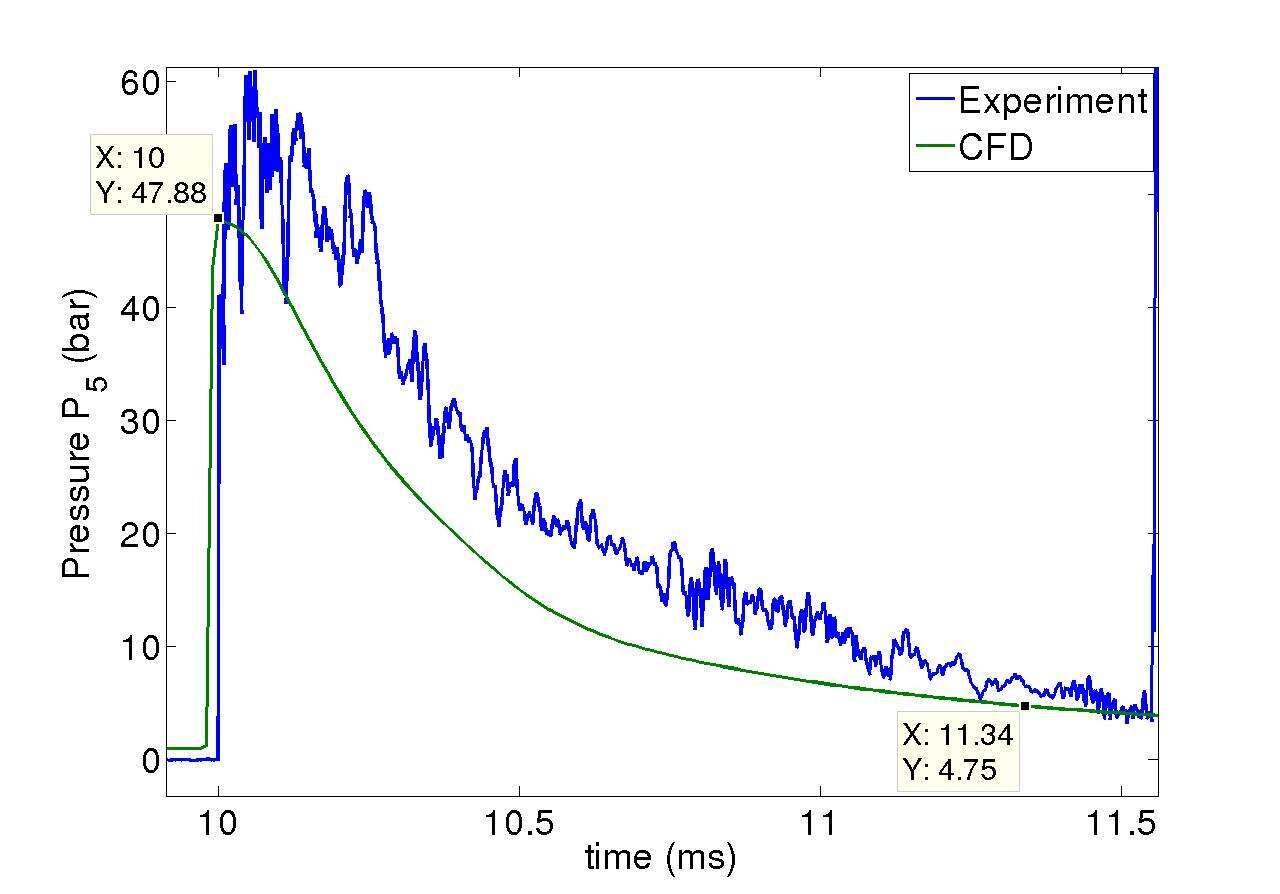
It is proposed to carry out some blast mitigation studies on Aluminum plates of various thickness. The effects of the pulse duration on the response of these plates would be studied.
From the current study, it has been concluded that this shock tube can be used to simulate blast events having pulse widths greater than 10 ms (1.2 ms times the scaling factor). Further details on the types of loading that may be simulated in this facility would be included in the full paper.
References:
1. M. Stoffel, R. Schmidt, D. Weichert , International Journal of Solids and Structures 38 (2001) 7659-7680
2. Norman Jones, Structural Impact, Cambridge University Press (1997)
3. http://www.un.org/disarmament/un-saferguard/kingery-bulmash/