This paper describes structural design method of a generic single strut scramjet combustor which is subjected to shock induced high temperature and high pressure loads in Mach 7 hypersonic flow at 30 km altitude. Multiple shocks across the mixed compression air intake reduce the Mach number to 2.2 and expose the scramjet to high temperature and high pressure. Thermal stress induced deformation becomes very significant in these high temperature flows causing coupled thermal-structural interaction [1], hence a coupled thermal-structural analysis becomes very crucial to designing a scramjet combustor. Coupled thermal-structural analysis of flying vehicles under high speed flow with shock induced loading has been studied in details by Thornton and Dechaumphai [1], Culler and Namara [2], Ho and Paull [3],Ho et al [4]. Life prediction of hypersonic structures has been attempted by Sobotka et al [5]. Another important aspect is the use of thermal barrier coatings on the combustion chamber walls to reduce heat loss and to keep temperature within the operational limits of available materials. Relevant work has been reported by Zhao [6]. A stiffened structure is required to limit the deformation because thermally induced deformation has significant effect on aerodynamic heating [1]. Hence, important design parameters for a structurally reliant design are the thickness and parameters related to thermal barrier coating, thickness of the airframe, stiffener spacing and weight of the system. Determination of these parameters involves an iterative process and a complete framework to address the iterative nature of this design problem needs to be evolved.
The first step in this process is the estimation of the pressure and the heat flux inside the scramjet combustor. This has been simulated in ANSYS FLUENT CFD software with supersonic inlet boundary condition. Also the CFD methodology to predict pressure and heat flux on combustor has been validated with available literature [7]. The heat flux distribution and pressure are then mapped to structural domain of combustor. In the second step, the mapped heat flux is applied in steady state heat transfer analysis. Steady state heat transfer analysis with radiation boundary conditions has been performed in ANSYS APDL as compared to a more realistic transient heat transfer analysis. This approximation leads to a higher temperature prediction in the present steady state analysis which further gives an engineering margin to the design. The temperature distribution obtained from the steady state heat transfer analysis and the pressure distribution has been applied to the combustor to perform a coupled 3-D static thermal-structural analysis by optimizing the constrain condition. The coupled thermal-structural analysis being iterative is performed by a novel automated design loop consisting of CAD modeller- PTC Creo, meshing software- HyperMesh and FEM solver- ANSYS APDL which seamlessly performs analysis by parametric variation of design variables. High fidelity structured hexahedral mesh is generated in HyperMesh and 20 node solid element, SOLID 226, with thermal as well as structural degree of freedom have been used for coupled thermal- structural analysis [8]. Another novelty is minimization of deformation for accurate modelling of aerodynamic heating and fluid flow around the scramjet combustor. This has been achieved by appropriate selection of design variables. Temperature dependent material properties have been used for coupled thermal-structural analysis and design of scramjet combustor . Figure 1.1 shows schematic of thermal-structural analysis and Figure 1.2 shows the structural design loop.
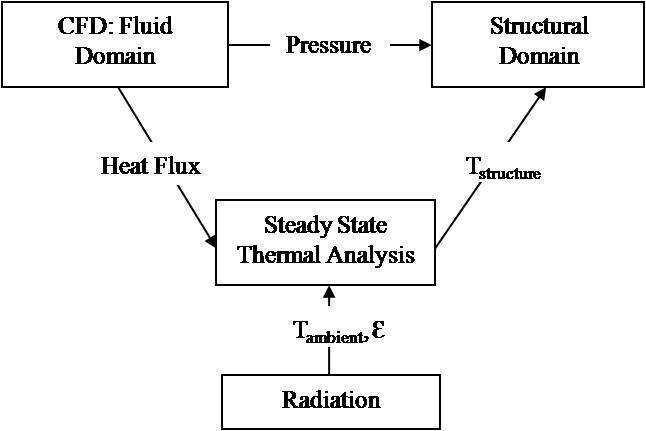
Figure 1.1 Thermal structural analysis scheme
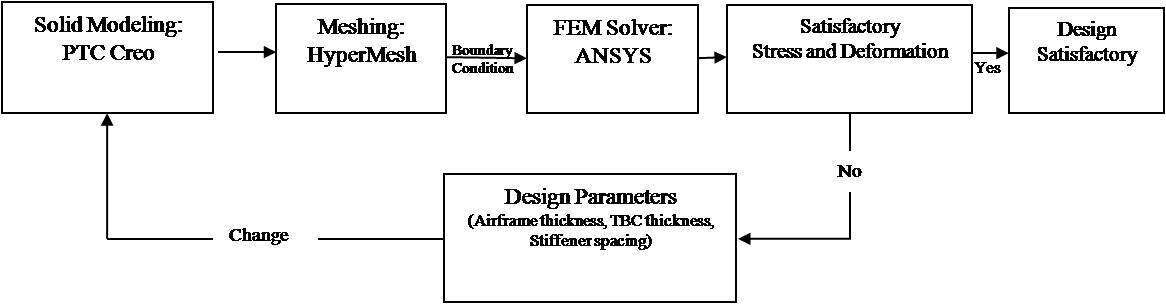
Figure 1.2 Structural design loop
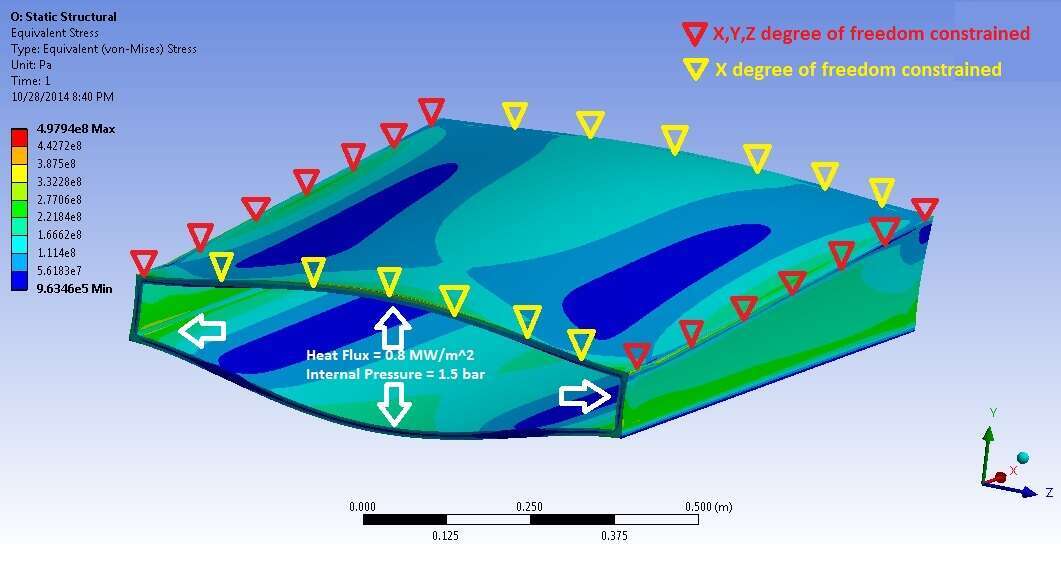
Figure 2 Coupled thermal structural analysis : Von Mises contours
Coupled thermal-structural analysis for a non-stiffened combustor with internal pressure of 1.5 bar and heat flux of 0.8 MW/m2, constrained along edges has been performed and its Von Mises stress contour plotted as shown in Figure 2. It has also been found that use of stiffeners reduce total deformation of combustor. A parametric variation of design parameters has been given to meet the objectives of minimizing deformation, weight and strength criteria of materials. A comparative study on the effectiveness of thermal barrier coatings of yttria stabilized zirconia, lanthanum zirconium oxide and other ceramics as material choice has been performed. The effect of stiffener spacing and panel thickness in reducing the stress and deformation of structure has been studied. Details of outcomes of simulation which will be discussed in the paper gives insight regarding body temperature vs. thickness of thermal barrier coating; body temperature vs. type of thermal barrier coating; stress and deformation map for various combination of material and geometric parameters.
Key words: Shock, Supersonic Flow, Thermal-structural analysis, Scramjet, Thermal Barrier Coating (TBC).
References
[1] Thornton and Dechaumphai, Coupled Flow, Thermal, and Structural Analysis of Aerodynamically Heated Panels, Journal of Aircraft, Vol. 25, No. 11, November 1988, Pages 1052–1059
[2] Adam J. Culler and Jack J. McNamara, Fluid-Thermal-Structural Modelling and Analysis of Hypersonic Structures under Combined Loading, 52nd AIAA Structures, Structural Dynamics and Materials Conference,4 - 7 April 2011, Denver, Colorado
[3] Ho and Paull, Coupled thermal, structural and vibrational analysis of a Hypersonic engine for flight test, Aerospace Science and Technology, Volume 10, Issue 5, July 2006, Pages 420–426
[4] Ho, Kotousov, Nguyen, Harding, Codrington and Hideaki Tsukamoto , FGM (Functionally Graded Material) Thermal Barrier Coatings for Hypersonic Structures – Design and Thermal Structural Analysis, Source: http://www.dtic.mil/dtic/tr/fulltext/u2/a474097.pdf, Accessed on October 18, 2014
[5] James C. Sobotka, Alpay Oral and Adam J. Culler, Towards a Coupled Loads-Response-Life Prediction Framework for Hypersonic Structures in Combined Extreme Environments, 54th AIAA/ASME/ASCE/AHS/ASC Structures, Structural Dynamics, and Materials Conference
[6] Hengbei Zhao, Low Conductivity Thermal Barrier Coatings, University of Virginia, Source:http://www.virginia.edu/ms/research/wadley/Thesis/HZhaoPhD.pdf, Accessed on October 20, 2014
[7] Tohru and Kouch, Flame structures and combustion efficiency computed for a Mach 6 scramjet engine, Original Research Article Combustion and Flame, Volume 142, Issue 3, August 2005
[8] ANSYS Documentation, Release 15.0