Introduction
Supersonic jets are used in the fields of aerospace, refrigeration and precision manufacturing. The supersonic nozzles in most cases result in compressible shear layers and the subsonic nozzles result in incompressible shear layers. The simple conical nozzles used at supersonic speeds result in comparatively slow spreading rates than subsonic nozzles. This is because the compressible shear layers have been observed to spread more slowly than the incompressible shear layers.
Supersonic nozzles having exotic shapes to enhance mixing have been developed. To enhance mixing the Elliptic Sharp Tipped Shallow (ESTS) lobed nozzle has been developed at LHSR, IISc, India . This unique nozzle has a profile with sharp tips sand eliptical lobes. This innovative structure produces streamwise vortices and azimuthal velocity components which must help in enhanced mixing and spreading . The ESTS 4 lobed nozzle has shown mixing enhancement compared to a conical nozzle designed for the same mach number [1].
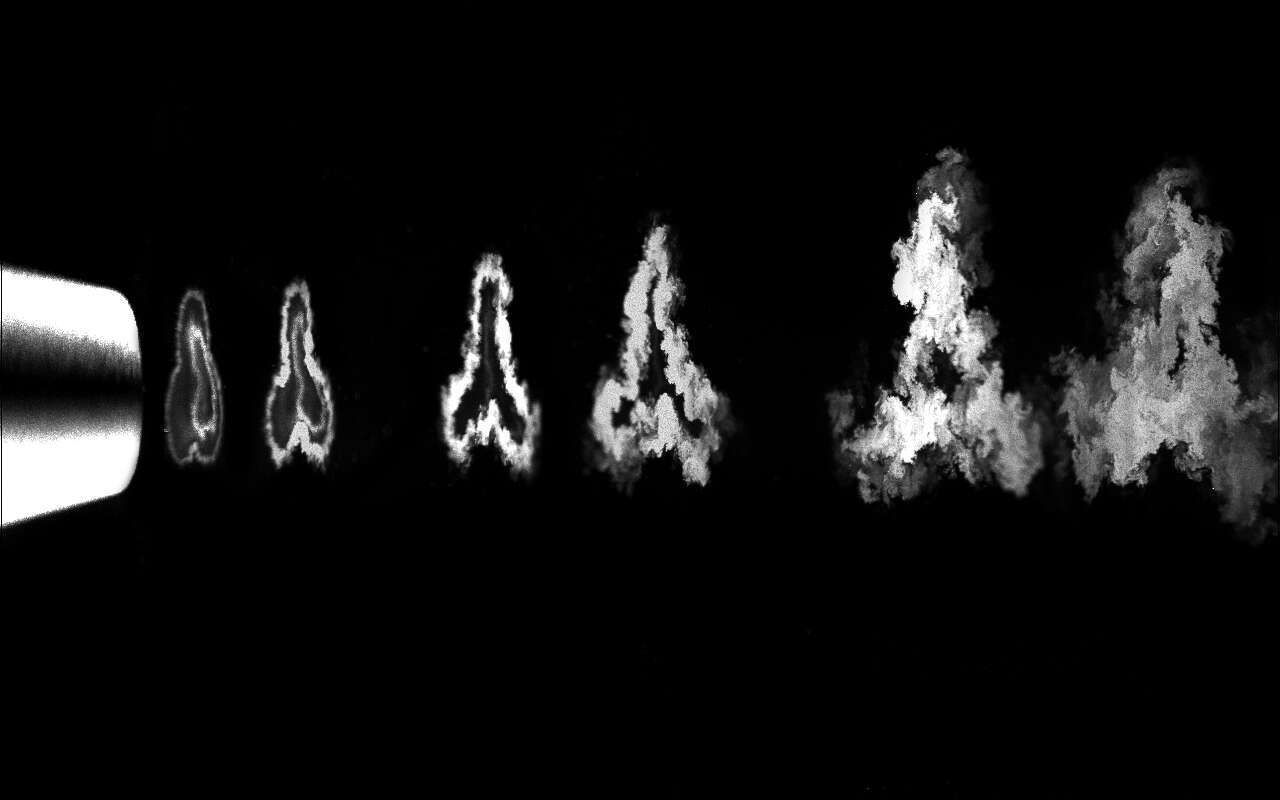
Figure 1: Laser scattering images of ESTS 3 lobed nozzle at 20, 40, 60, 80, 100 and 140 mm from nozzle exit
The laser scattering image clearly illustrates that the flow coming out of an ESTS lobed nozzle is three dimensional. This study will try to resolve t density he velocity and fields of the flow from the ESTS lobed nozzles.
Experimental Setup:
Nozzle:
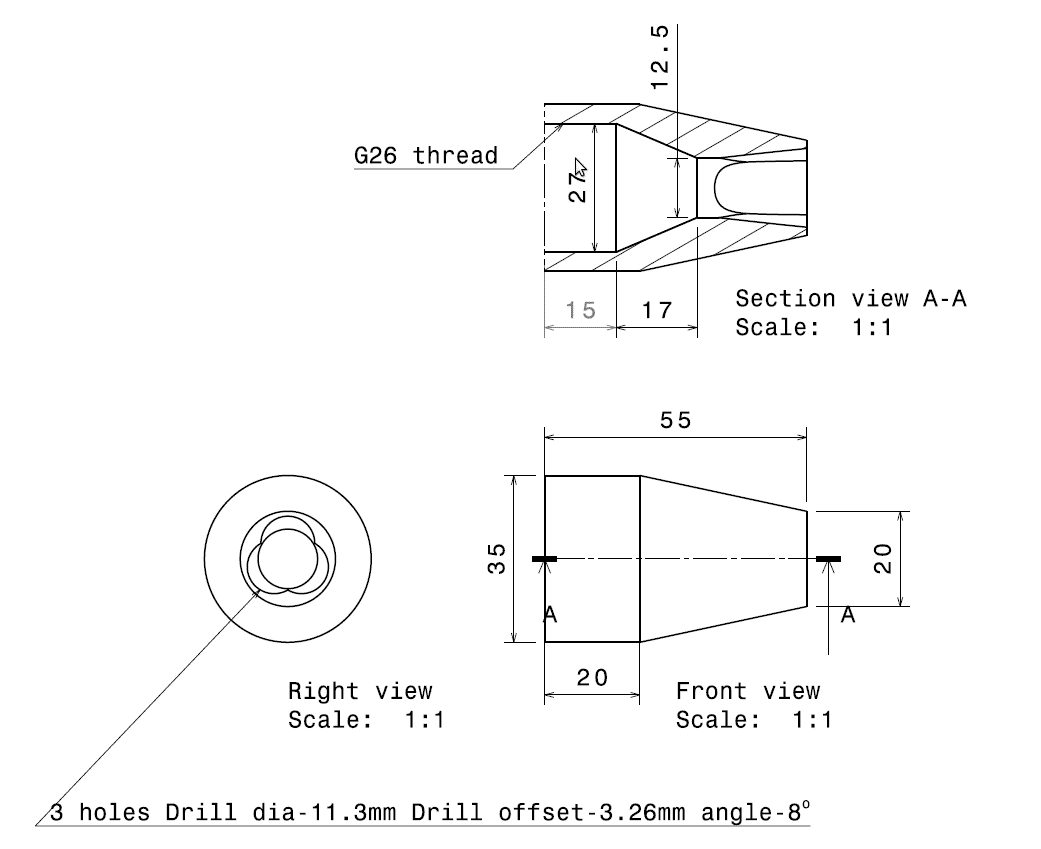
Figure 2: Orthogonal views of the ESTS 3 lobed nozzle
The nozzle flow is delivered from three compressed air tanks (1 x 3 m3 @12 bars and 2 x 6 m3@12 bars) to a stagnation chamber. This is connected to the supersonic nozzle by a short straight pipe. Experiments will be done on nozzles with different numbers of lobes designed for various mach numbers at various stagnation pressures. The conical nozzle is designed with a particular throat diameter for a particular exit mach number. The ESTS lobed nozzle is designed such that the total exit area remains the same as that of the conical nozzle. Thus according to isentropic area relations the average exit Mach number is the same.
Figure 3: Block diagram of the experimental setup for Stereo PIV
Experimental Methodology:
Particle Image Velocimetry (PIV):
Stereo PIV measurements will be carried out at different axial locations from the exit of the nozzle. An Nd-YLF laser of wavelength 532 nm @ 24 mJ per pulse is used for illumination. Phantom M110 having the resolution of 1MPixel is used for capturing the image. The laser is allowed to pass through a light arm to form a light sheet of thickness 1mm. Double exposed images will be acquired using the LaVISION DaVIS® software which synchronises the laser and the camera. The flow seeding is done using the laskin nozzle, which produces a particle diameter of 1µm.
Background Oriented Schlieren (BOS):
Background Oriented Schlieren (BOS) will be used to capture the density field of the flow. The nozzle will be rotated in 5° steps corresponding to 72 view angles to capture the three dimensional density field. The image will be captured using the Phantom V310 camera having a resolution of 1MPixel. The illumination of the background dot pattern is provided using a Pal Flash which has a pulse duration of 1µs. The post processing steps used to get the three dimensional density field is given by Venkatakrishnan and Suriyanarayanan [2].
Experiments will be conducted and the results will be published in the full paper.
References
-
S. Rao and G. Jagadeesh, "Novel supersonic nozzles for mixing enhancement in supersonic ejectors," Applied Thermal Engineering, vol. 71, no. 1, pp. 62-71, 2014.
-
Venkatakrishnan, L and Suriyanarayanan, P (2009) Density field of supersonic separated flow past an afterbody nozzle using tomographic reconstruction of BOS data. Experiments in Fluids . pp. 463-473. ISSN 0723-4864