The Supersonic Combustion RAMJET (SCRAMJET) engine proposed by F.S.Billig in 1964 has been perceived as the most hopeful air breathing propulsion system for the hypersonic flight (Mach >5). The nozzle plays a vital role in accelerating heated air from the combustor to produce thrust in a scramjet engine. The design of nozzle is critical in obtaining necessary thrust margins to perform accelerated flights. Single expansion ramp nozzles are generally used in hypersonic cruise vehicle powered by scramjet engines to produce the necessary thrust and are two dimensional in nature. The availability of literature for design of two dimensional contoured scramjet nozzles are scarce. Moreover there is a necessity for use of high fidelity models in designing the nozzle which help in reducing the uncertainties that appear on the force estimations. Hence, in the present study a design methodology has been established using automated high fidelity CFD process to estimate the thrust of two dimensional contoured nozzle and in turn arrive at thrust optimized nozzle contour for a scramjet engine using Artificial Neural Network(ANN) and Teaching Learning Based Optimization algorithm (TLBO) [1] (Figure 1). An in-house developed Python script is used for the automation process. The nozzle geometry used in this method consists of inner surface which is defined by a circular arc and then followed by a cubic spline curve and the outer surface is defined by a cubic spline curve. The parameters considered for the geometry creation are combustor gradient (θc), nozzle entrance arc angle (θa), nozzle entrance radius (ra),nozzle length (L), nozzle height (H), nozzle inlet height (h), thickness at the base (t), inner trailing edge gradients (θb,θd) and outer trailing edge gradient (θe) (Figure 2). A two dimensional structured mesh is generated using Ansys ICEM CFD script. Two dimensional implicit Reynolds Averaged Navier–Stokes (RANS) simulation with k-ω model is carried out using HIFUN, to obtain the thrust. The CFD process is being validated using results from available literature [2]. Preliminary Euler simulation over a coarse 2D grid (42396 elements - Figure 3) shows reasonable agreement qualitatively (Figure 4). RANS computations and grid independence study are being carried out to bring down the error margin and computational time. The CFD solutions obtained for a given set of geometric variables are trained and tested to arrive at a meta model using ANN. The meta model is used by TLBO algorithm to obtain an optimized nozzle contour parameters. The optimisation is carried out for a hypersonic cruise vehicle nozzle designed to fly at Mach number of 6 and altitude of 30km. The effect of the geometric variables over the objective function obtained will be presented. The methodology established here, using in house developed scripts, parallel computations and state of the art evolutionary algorithms can be used as an effective design tool to obtain optimized two dimensional nozzle contours for hypersonic cruise vehicles.
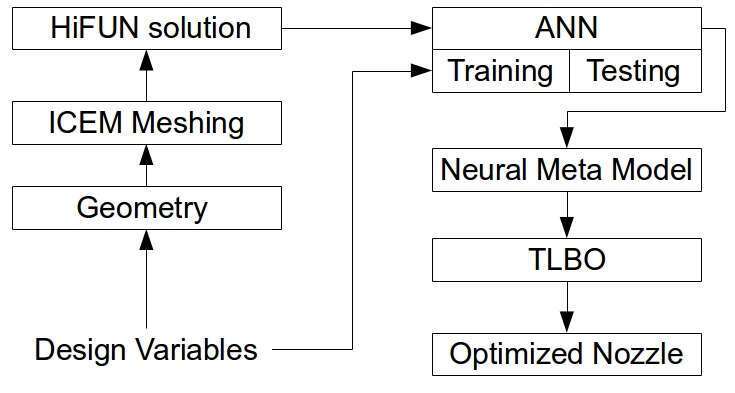
Figure 1: Flowchart depicting the complete optimization process.
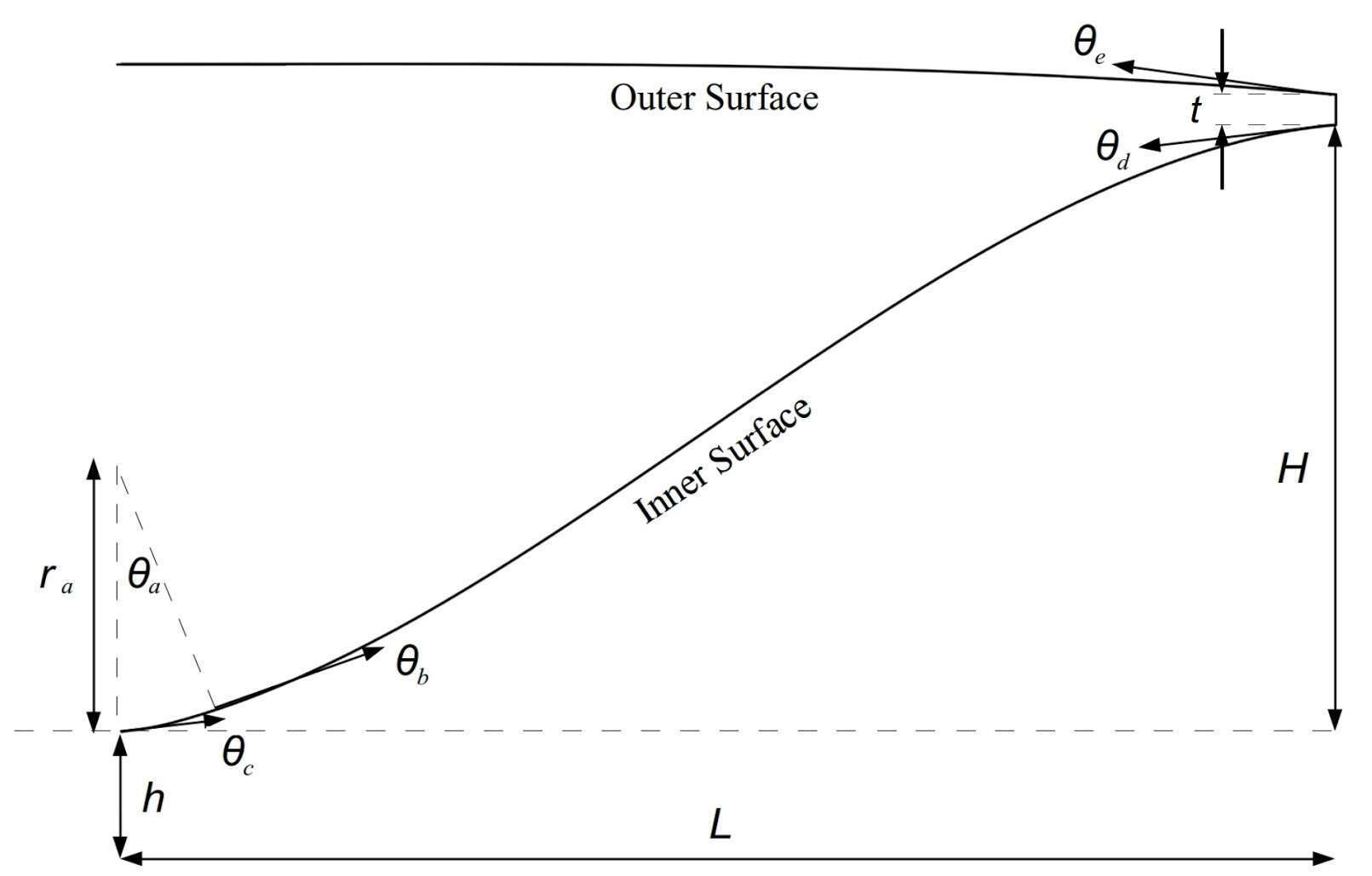
Figure 2: Scramjet nozzle geometry
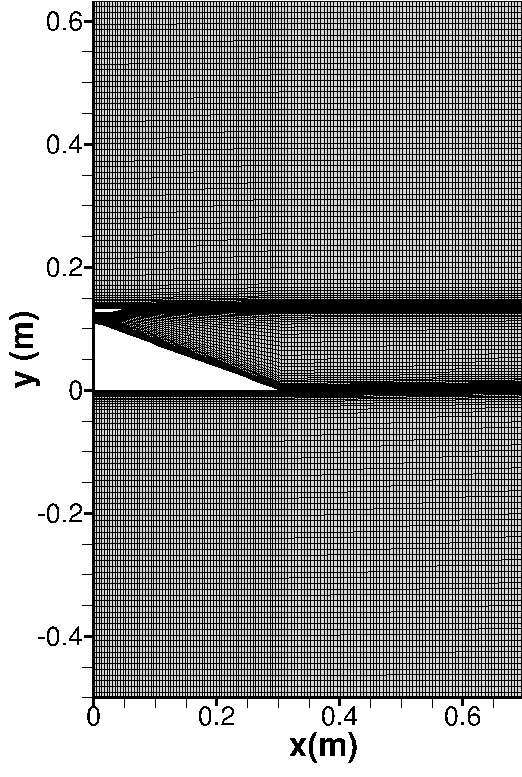
Figure 3: Computational domain for validation case.
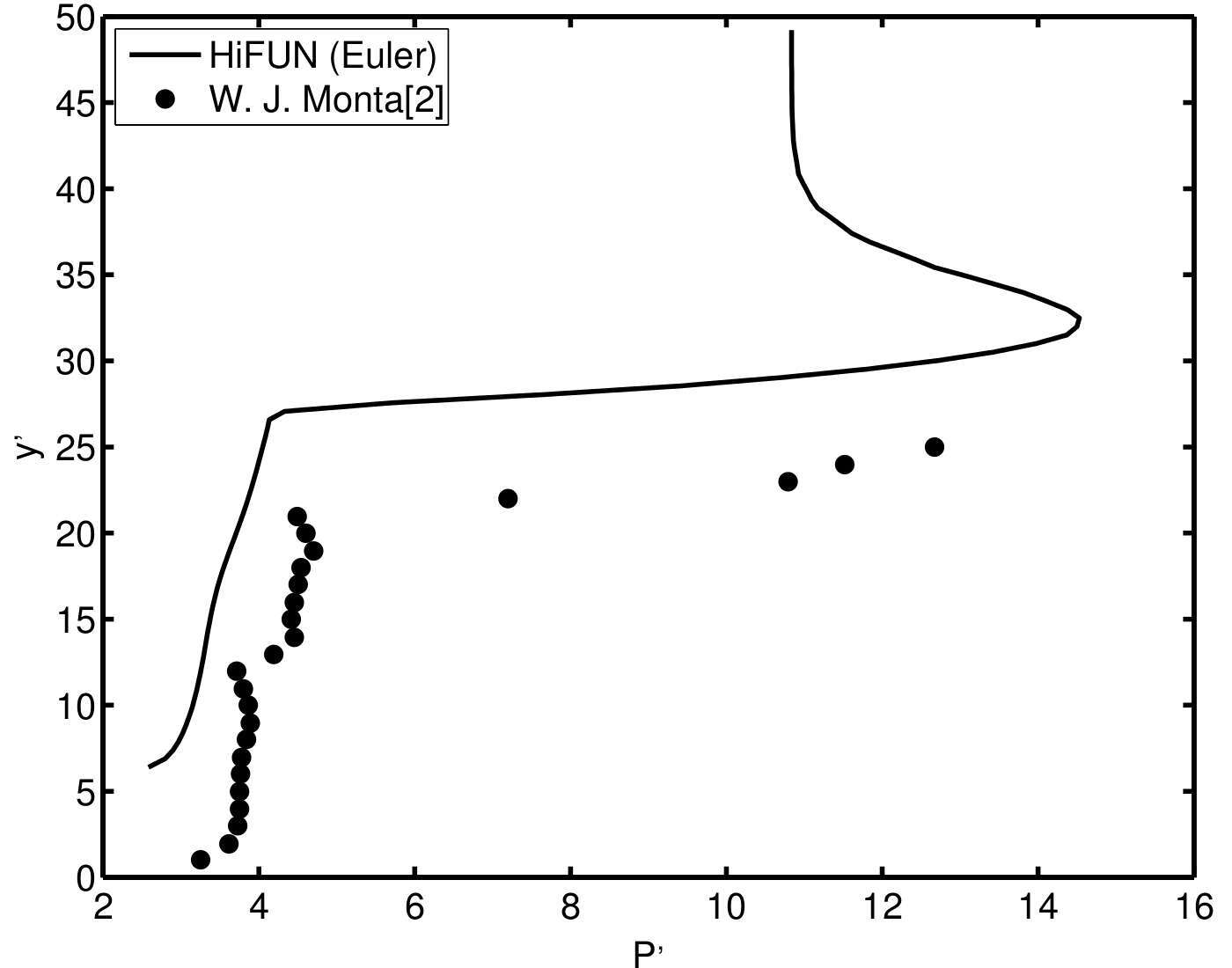
Figure 4: Pressure comparison between numerical and experimental data.
Reference:
-
R. Venkata Rao and Vivek Patel, “ An elitist teaching-learning-based optimization algorithm for solving complex constrained optimization problem.” International Journal of Industrial Engineering Computations 3 (2012) 535-560.
-
W.J. Monta, Pitot Survey of Exhaust Flow Field of a 2-D Scramjet Nozzle at Mach 6 With Air or Freon and Argon Used for Exhaust Simulation, NASA TM-4361 (1992).