Fundamental studies on the rapid boiling of liquids have been carried out for many years in connection with nuclear power plant severe accidents [1] and BLEVEs [2]. Small-scale experiments have been carried out to investigate evaporation wave propagation at the superheat limit by thermally heating a liquid drop to the superheat limit [3, 4]. Evaporation wave propagation at the superheat limit has also been studied by the rapid depressurizing of the liquid in a glass tube [5-7]. At the superheat limit molecular fluctuations spontaneously produce nucleation sites where evaporation originates and spreads as a wave through the rest of the liquid.
Experiments have recently been performed with liquid CO2 at room temperature in an acrylic vertical cylinder to observe the boiling process that takes place when the cylinder is suddenly depressurized from one end into the atmosphere [8]. Unlike in the superheat limit experiments performed in [5-7] the boiling that results from the depressurization of the liquid in a polycarbonate tube is expected to be heterogeneous due to the many nucleation sites available at the walls. High-speed front-lit photography was used to capture the boiling in the CO2 liquid, and pressure transducers were used to measure the depressurization of the cylinder.
In the present experiment the shock wave generation from rapid expansion driven evaporation of liquid CO2 is studied in a vertical shock tube as shown in Fig. 1. The driver section, initially containing the liquid CO2, consisted of a transparent 480 mm long, 16 mm inner-diameter polycarbonate tube. Visualization of the evaporation is captured with a Phantom v12 camera operated at 20,000 fps with backlighting. The cylinder is placed inside of a square acrylic channel filled with circulating water. The CO2 liquid initial temperature is set by the water temperature. The surrounding water also reduces image distortion caused by the cylinder curvature. The driven section consisted of a 1.16 m long, 16 mm inner-diameter stainless steel tube that contains nitrogen. An aluminum diaphragm separates the driver and driven sections. The 10 micron thick grade 1100 aluminum alloy used for the diaphragm consistently bursts at roughly 51 bar, roughly equal to the saturation pressure of CO2 at 15 oC, without the use of an arrow point that obstructs the flow. An experiment is carried out by loading solid CO2 (dry ice) into the driver, the diaphragm is placed into position and the driven section is fastened to the driver. As the solid CO2 slowly heats up it melts forming a stratified layer of liquid and vapor. The pressure rises until the diaphragm bursts initiating the rapid depressurization of the vapor, followed by the depressurization and boiling of the liquid layer. The height of the liquid layer was varied and the pressure-time history was recorded at four locations shown in Fig. 1. The position of the pressure transducers relative to the driver endwall are: P1- 0 mm, P2- 419 mm, P3- 584 mm, P4- 1403 mm.
Figure 2 shows images of the driver taken at a framing rate of 20,000 frames per second in a test with a 240 mm layer of liquid CO2 (striped background is for reference). The diaphragm bursts at a pressure of 51 bar and an expansion wave propagates downward (not visible in Fig. 2) isentropically cooling the saturated vapor. The expansion wave reflects off the CO2 liquid surface and also continues to propagate through the liquid CO2. A short time after the expansion wave reflects off the liquid surface, heterogeneous evaporation starts at the liquid surface. An evaporation front (vaguely discerned in Fig. 2) propagates down the liquid column and the resulting two-phase mixture expands in the opposite direction (the top of the two-phase mixture can be seen as the transition from the dark to the transparent).
The pressure traces obtained for a test with a 14.3 cm layer of liquid CO2 are provided in Fig. 3. For comparison the pressure traces obtained with the driver completely filled with CO2 vapor are provided in Fig. 4. Time-zero for the pressure traces is arbitrary as there is no measurement of the diaphragm time of diaphragm. The pressure plateau observed in P2 during the expansion process is caused by a Teflon seal that protrudes about 1.5 mm into the shock tube just below the diaphragm. In the driver the effect of the CO2 evaporation is manifested in Fig. 3 by the leveling off of the pressure recorded at P1 starting at 4.5 ms and the sudden pressure rise observed at 7.0 ms in P2. The CO2 evaporation does not influence the shock wave generated in the driven section but does cause a strong pressure rise at P3 starting at 8.0 ms and to a lesser extent at P4 starting at around 10.5 ms. We are in the process of correcting the protruding seal, after which time a complete set of data with different CO2 liquid levels and temperatures will be obtained.
References
1. Ciccarelli, G. and Frost, D.L., Fragmentation Mechanisms Based on Single-Drop Experiments Using Flash X-Ray Photography, Nucl. Eng. Design, 146, pp, 109-132, 1994
2. Voort, M.M., Berg, A.C., Roekaerts, D.J.E.M., Xie, M. and Bruijn, P.C.J., Blast from explosive evaporation of carbon dioxide: experiment, modeling and physics. Shock Waves 22:129-140 (2012).
3. Shepherd, J.E. & Sturtevant, B., 1982. Rapid evaporation at the superheat limit. J. Fluid Mechanics, 121: 379–402 (1982).
4. Frost, D.L. Dynamics of explosive boiling of a droplet. Physics of Fluids, 31(9): 2554–2561 (1988)
5. Hill, L.G.: An experimental study of evaporation waves in a superheated liquid. Dissertation (Ph.D.), California Institute of Technology (1990).
6. Simoes-Moreira, J.R and Shepherd, J.E., Evaporation waves in superheated dodecane, J. Fluid Mech. 382:63-86 (1999).
7. Kuznetsov, V.V., Kozulin, I. A. and Vitovsky, O.V., Experimental Investigation of Adiabatic Evaporation Waves in Superheated Refrigerants, Journal of Engineering Thermophysics 21 (2):136–143 (2012).
8. Tosse, S., Vaagsaether, K. and Bjerketvedt, D. An Experimental Investigation of Rapid Boiling of CO2, ICDERS (2013).
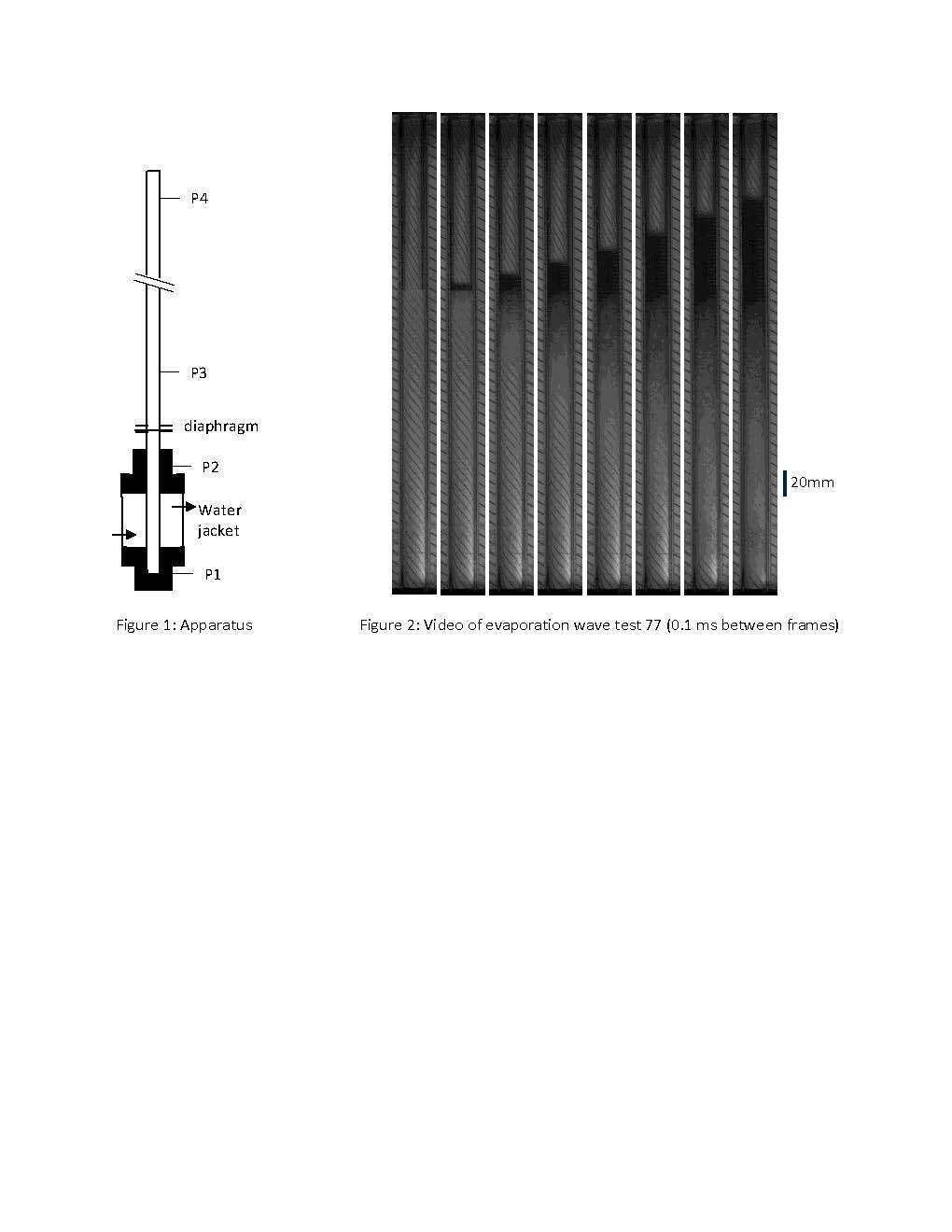
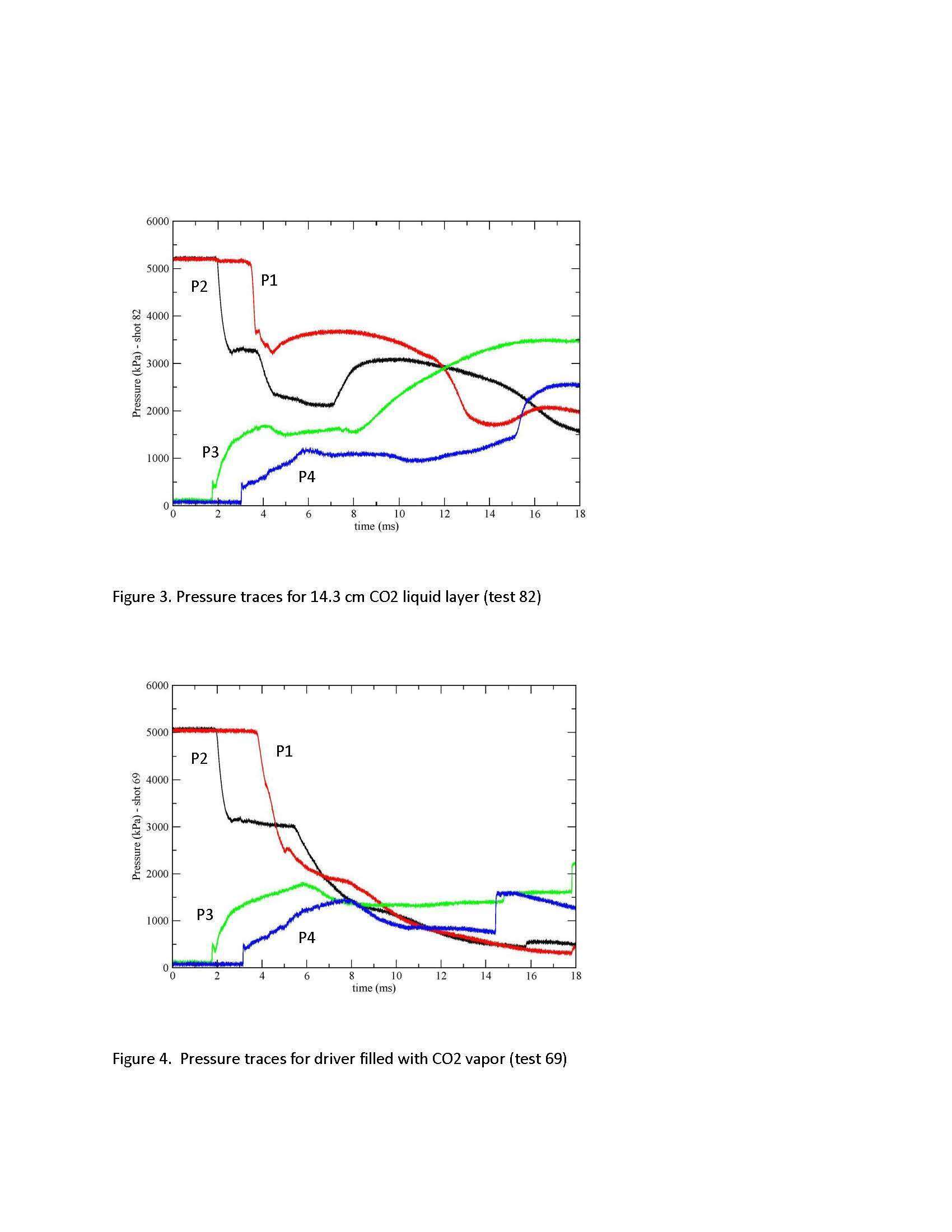