During the last two decades several design approaches have been pursued in order to enhance performance of machine tools. The first approach is the design of Parallel Kinematic Mechanisms (PKMs), Fig. 1, which are known for their high stiffness and accuracy [1]. The second approach is the design of reconfigurable mechanisms, in which given a task, performance are enhanced through reassembly of the structure. The third approach is the design of redundant mechanisms that have more than the minimal number of degrees of freedom that are required for the task. Combing the three approaches led to the design of Redundant Reconfigurable PKMs (RR-PKMs), in which redundancy can be utilized to ameliorate performance, on the one hand through reconfiguration without the disassembly of the structure, and on the other hand through tool-path optimization.
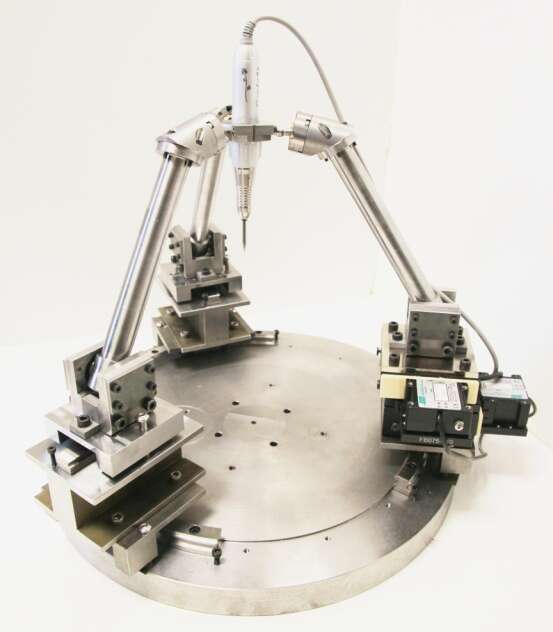
Figure 1. A prototype of a new 3×PPRS PKM that was developed at our laboratory.
In order to design a RR-PKM based tool-holder, a new design methodology was developed [2]. The methodology is based on a multi-tiered optimization that considers the redundant reconfigurability effect on performance. The objective of the methodology is to determine the mechanism`s topology, redundancy, design variables, and configurations that attain the best performance. Implementing the methodology led to the design of a novel three chains RR-PKM that can reconfigure into lower mobility sub-configurations, working mode configurations, and several sub-PKMs that differ in topology, Fig. 2.
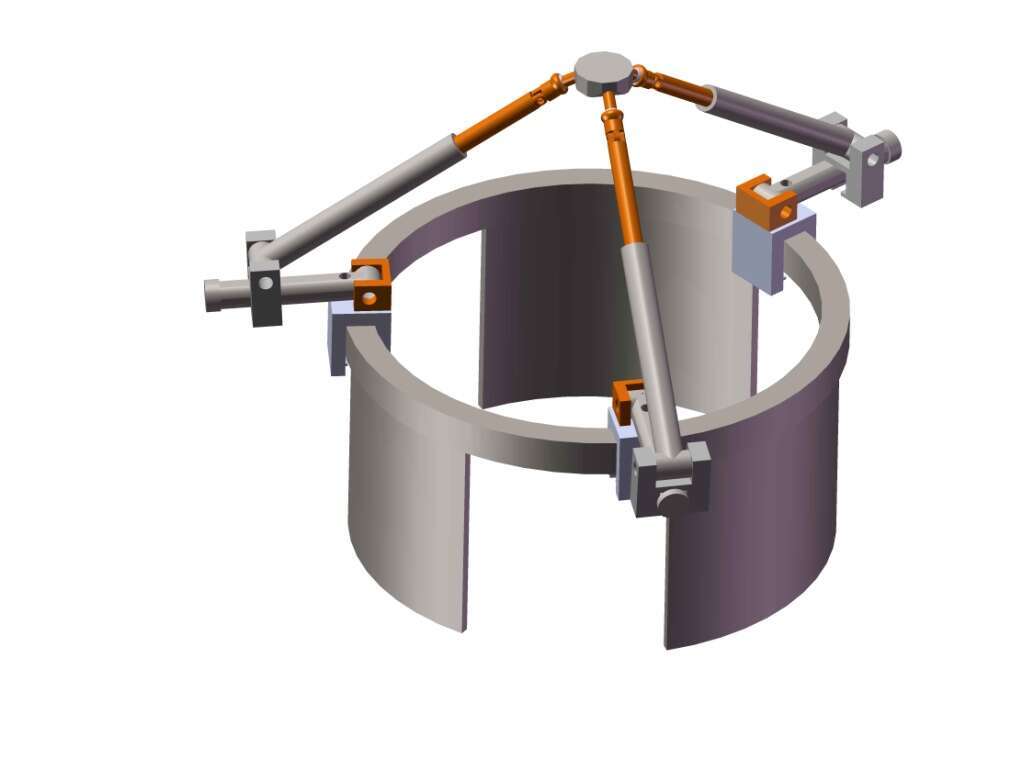
Figure 2. A CAD model of the new 3×PRPRS RR-PKM.
[1] H. Azulay, M. Mahmoodi, R. Zhao, J. K. Mills, and B. Benhabib, "Comparative analysis of a new 3×PPRS parallel kinematic mechanism," Robot Cim-Int Manf, vol. 30 pp. 369–378, 2014.
[2] H. Azulay, J. K. Mills, and B. Benhabib, "A Multi-Tier Design Methodology for Reconfigurable Milling Machines," Journal of Manufacturing Science and Engineering, vol. 136, pp. 0410071-10, 2014.