Undesired vibrations of high speed rotating systems due to imbalance is an inevitable physical phenomenon. In the absence of radial asymmetry, the steady state response of the rotor system is a synchronous circular whirling motion. In this motion, the shaft cross section center of gravity is moving in a circular orbit around the center of rotation. Under these conditions, the rotor’s mass elements do not carry relative acceleration and thus the flexible rotor can be regarded as a rigid (and bent) rotor.
Active magnetic bearings (AMBs) utilize electromagnetic forces and magnetic levitation principals to allow rotation with zero mechanical friction. The advantages of AMBs over traditional rolling-element bearings are significant and includes: spin with no contact, applicability to systems under vacuum conditions and a maintenance-free nature. The AMB air gaps (between the rotor and stator) are actively controlled and are utilized, in this research, for inertial centering, which consequently eliminates undesired vibrations due to rotor imbalance.
The general idea is to constrain the motion of the rotor to rotate about its principal axis of inertia and through its center of mass. This is achieved by the inertial centering control law which, in a rigid rotor case, results in zero gyroscopic forces and zero radial forces. However, in a flexible rotor case, the latter is valid only when the rotor reaches a steady-state motion, in which the rotor’s mass elements do not carry relative acceleration. In order to reach this type of steady state motion, an artificial damping is added to the control scheme in order to dissipate stored elastic energy in the flexible rotor.
Simulation results show a complete suppression of synchronous imbalance forces and moments as the desired inertial centering was successfully achieved as illustrated in the figure below.
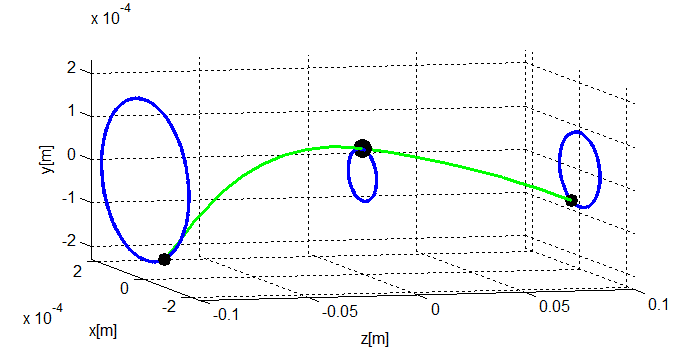